What is a CNC Machine Tool?
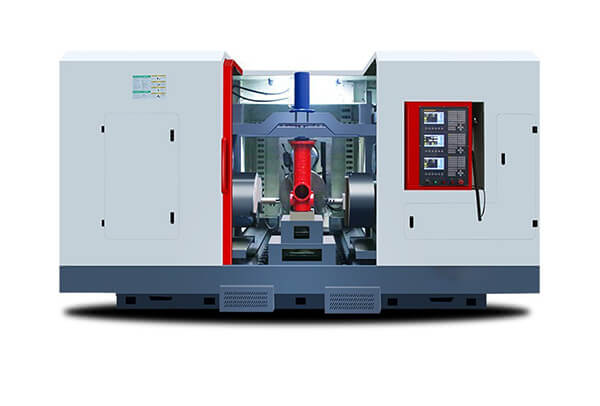
Machine tools are crucial devices employed for metal processing operations such as cutting, shaping, and grinding in the manufacturing industry. These tools play a pivotal role in producing diverse workpieces and components.
The primary function of machine tools is to transform raw materials into workpieces with specific shapes and dimensions. This is achieved through cutting, drilling, milling, grinding, and bending workpieces utilizing rotating, moving, or fixed tools. Machine tools typically comprise mechanical structures, transmission systems, control systems, and auxiliary devices.
There are various classifications of machine tools, including:
- Lathe: This tool rotates workpieces and performs cutting operations, suitable for cylindrical workpieces.
- Milling machine: It conducts cutting operations on workpieces using rotating tools, capable of achieving flat, curved, and complex shape machining.
- Drilling machine: This tool is used for drilling operations, cutting into workpieces using rotating drill bits.
- Grinding machine: It is employed to grind workpieces, enhancing their smoothness and precision.
- Shearing machine: This tool cuts metal sheets, pipes, and other materials.
- Punching machine: It is used for metal stamping operations, creating parts and assemblies.
The evolution of machine tools is closely intertwined with numerical control technology. Modern machine tools commonly utilize Computer Numerical Control (CNC) technology, where pre-programmed instructions control the machine’s motion and operations, enhancing precision, efficiency, and automation.
As industries demand higher processing precision and efficiency, machine tools have transitioned from standardized, single-function machines to multi-functional, multi-station, non-standardized, and customizable machining centers.
How are Machining Centers Classified?
Machining centers integrate multiple processing functions like milling, drilling, and tapping into one device. They can be categorized based on different criteria:
- Bed Structure: Machining centers are classified as vertical or horizontal. Vertical machining centers have a vertical spindle, suitable for smaller workpieces, while horizontal machining centers have a parallel spindle, suitable for larger and heavier workpieces.
- Number of Spindles: They can be single-spindle or multi-spindle. Single-spindle centers complete one type of machining operation at a time, whereas multi-spindle centers perform multiple operations simultaneously, increasing efficiency.
- Control System: Machining centers are categorized as Numerical Control (NC) or Computer Numerical Control (CNC). CNC machining centers offer advanced functions and flexible programming methods.
- Number of Feed Axes: They can have three, four, five, or more axes, enabling machining of simple to complex surfaces.
Additionally, there are other classification methods, such as tool magazine-type, gantry-type, and moving-column-type machining centers, based on specific processing needs and requirements.
CNC machining centers, known for their intelligence, precision, and efficiency, meet the evolving needs of modern industry and are favored by high-tech companies.
What is a CNC Machining Center?
A CNC machining center is a high-precision and high-efficiency equipment controlled by a computer numerical control system. It integrates multiple processes like milling, drilling, tapping, and chamfering to complete various complex-shaped workpiece machining.
Key features of CNC machining centers include:
- High Precision: CNC machining centers achieve high-precision machining, ensuring dimensional accuracy and surface quality of workpieces.
- High Efficiency: They have automated functions like tool changing and automatic clamping, enabling continuous and high-speed machining, improving production efficiency.
- Versatility: CNC machining centers can perform various processes, suitable for machining complex-shaped workpieces.
- Flexibility: Controlled through programming, they provide high flexibility to meet diverse machining needs.
- High Automation: CNC machining centers achieve automatic tool changing, reducing manual intervention and enhancing machining consistency and stability.
Future Trends in CNC Machine Tools
CNC machine tools are moving towards intelligent development, emphasizing automation, intelligent decision-making, and predictive capabilities. They aim for higher precision, faster processing speeds, multifunctionality, multi-station capabilities, and flexible production. Integration with networking, cloud services, and emphasis on environmental protection and energy efficiency are also key trends.
Applications of CNC Machining Centers
CNC machining centers, controlled by computer numerical control systems, precisely perform various operations like milling, drilling, tapping, and chamfering, enabling high-precision and high-efficiency machining. These centers find extensive applications in aerospace, automotive manufacturing, mold making, and mechanical processing industries, playing a vital role in modern manufacturing processes.