Hardfacing Machine
At Deewi Automation, we are committed to bringing revolutionary progress to the industrial manufacturing field through high-end plasma cladding technology. Our range of plasma cladding machines represents our latest achievements in precision manufacturing and innovative solutions designed to meet your highest requirements for efficiency, precision and reliability.
Innovative technology, excellent performance.
Our plasma cladding machines use the most advanced technology to provide uniform and precise coverage on a variety of metal surfaces, significantly improving the wear resistance, corrosion resistance and service life of the workpiece. Whether it’s complex industrial components or precision manufacturing needs, Deewi’s welding machines provide unparalleled solutions.
Types of Hardfacing Machines:
- Based on the type of heat source used, they can be divided into:
- Laser Cladding Machines: These use high-energy lasers as the heat source and can precisely control the welding speed and intensity, achieving high-precision and high-quality welding results. The equipment is relatively expensive and is commonly used where high precision and batch production are required.
- Plasma Transferred Arc Welding Machines: Using a plasma arc as the heat source, they can also control the welding speed, current, and voltage precisely for high-quality welds. The equipment is cost-effective and flexible to use. Plasma arcs have high energy density and are commonly used for high-energy welding applications, such as repairing workpieces with high hardness and high melting points.
- Based on the degree of automation, they can be classified into:
- Automated Hardfacing Machines: These feature automated control systems and welding robots or mechanical arms that can precisely control welding speed, current, voltage, and path. They offer good welding precision and consistency, low labor costs, and are suitable for large-volume, standardized hardfacing tasks.
- Manual Hardfacing Machines: These belong to the traditional hardfacing methods, where welding quality heavily depends on the operator’s skill and experience. They are less consistent than automated welding but are very cost-effective and flexible in use.
- Based on equipment size and application scenario, they can be categorized into:
- Large Hardfacing Machines: Mostly used for batch production and repair, generally highly automated with high welding efficiency, and low reliance on labor. Suitable for large enterprises engaged in batch welding operations.
- Mobile Hardfacing Machines: Commonly seen with small to medium-sized equipment, featuring a mobile design for easy transport and movement, offering greater flexibility, though with limited automation and stability.
- Portable Hardfacing Machines: Compact design, simple in structure, extremely convenient for on-site repairs, allowing for in-situ repairs without disassembly. Often used for on-site repair work of machinery and equipment parts.
The above are only a few of the commonly seen machine types and not an exhaustive list.
Applications and Usage Scenarios of Hardfacing Machines:
- Repair and Maintenance: Hardfacing can repair worn parts, restoring their original size and shape. For example, the production and repair of parts like bucket teeth, blades, bearing housings, bearings, hydraulic cylinders, piston rods, gears, racks, rotating shafts, and couplings in construction machinery.
- Adding Wear-Resistant Layers: Adding wear-resistant layers to the surface of newly manufactured workpieces can reduce material costs and extend their service life, such as applying hardfacing materials to the hammers and blades of mining machinery.
- Enhancing Impact Resistance: For parts that need to withstand strong impacts, like hammerheads and crusher arms, hardfacing can improve their impact resistance.
- Extending Service Life: For consumable parts, such as metal rollers and wheels in conveyor systems, hardfacing can significantly enhance their wear resistance and service life.
- Imparting Special Properties: For parts requiring corrosion resistance, high-temperature resistance, or other special properties, selecting the appropriate hardfacing material can endow the workpiece with the needed characteristics.
Hardfacing Machines are extremely widely used across various industries and, with the continuous development of new processes and technologies, are replacing traditional processes in many fields. They improve the reliability, safety, and economy of equipment, reducing costs and energy consumption, and are becoming an indispensable tool in modern industry.
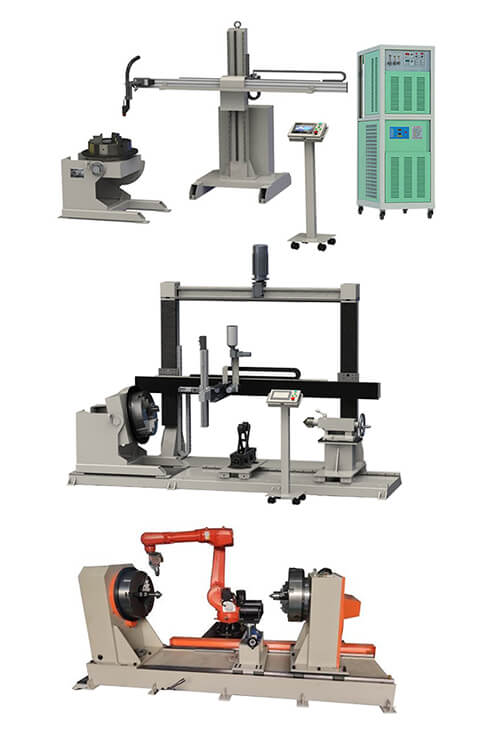
Quick Q&A – About Hardfacing Machine.
When using or maintaining Hardfacing Machines, users often encounter a range of issues. Below are some common questions and their corresponding answers:
Hardfacing Machine Process&Applications
Here are more cases and technical information available. If you have any further questions, feel free to contact us for further discussion.