Laser Cladding Machine
Deewi Automation: Your Premier Manufacturer, Supplier, and Exporter of High-Quality Laser Cladding Machines.
What is Laser Cladding Machine?
As the name suggests, the Laser Cladding Machine utilizes lasers to harden the surface of workpieces. Laser cladding involves the use of a high-energy-density laser beam to melt welding materials and the substrate surface, achieving surface hardening. It’s worth noting that typical laser welding results in a weld layer thickness ranging between 0.020 inches to 0.06 inches per operation. When multiple weld layers are stacked to form a three-dimensional geometric shape, we generally refer to it as a cladded layer. Compared to Plasma Hardfacing technology, Laser Cladding Machines offer a more concentrated heat source, leading to faster heating and cooling, a smaller heat-affected zone, and a lower dilution rate of the cladded layer, which can be more material-efficient. Laser Cladding often produces superior melting effects between different materials, creating unique microstructures in the cast area. As a result, laser cladding processes typically do not require annealing and are less prone to deformation. Laser Cladding Machines can further be categorized into powder-based Laser Cladding Machines and wire-based Laser Cladding Machines.
What is the difference between the Powder Laser Cladding Machine and the Wire Laser Cladding Machine.
When we refer to ‘powder’ and ‘metal wire’, we’re primarily discussing the distinct welding materials used by the Laser Cladding Machine. The powder option offers a richer variety of materials, hence Laser Cladding Machines often employ alloy powders as the preferred welding material. In the laser cladding process, these alloy powders are delivered to the center of the laser beam either coaxially or off-axially. Coaxial feeding typically suits the remanufacturing of workpieces with three-dimensional shapes, while off-axis (or off-center) feeding is generally reserved for large-area cladding tasks. In contrast, machines that utilize metal wires benefit from the wire’s continuous feed, and since the wire can fully melt within the molten pool, material utilization tends to be higher. Powder-based processes usually achieve around 85% material utilization. For vertical operations, we particularly recommend wire-based laser cladding machines, as they’re also adept at reconstructing the internal structures of workpieces. If you’re uncertain about which equipment or material to choose, Deewi Automation is always here for a discussion.
The composition of the Laser Cladding Machine.
As illustrated in the diagram, a basic Laser Cladding Machine typically consists of guide rails, a positioner, clamps, a laser torch, a laser generator, a powder feeder, a Gas Supply System, a cooling system, an exhaust system, a safety protection system, and an intelligent control system. The laser generator is the heart of the Laser Cladding Machine, providing the high-energy laser source required for laser cladding. Its performance dictates the capabilities of the entire machine. The laser torch emits both the laser beam and powder to complete the cladding process, significantly influencing the cladding results. The control system adjusts the movement of either the workpiece or the laser torch, ensuring precise control over the speed and accuracy of cladding. Of course, the above description merely provides a simple overview of the structure of the Laser Cladding Machine. These machines are typically custom-built. We customize each machine based on the specific requirements and budget of our clients. If you’re interested in this, please don’t hesitate to contact Deewi Automation.
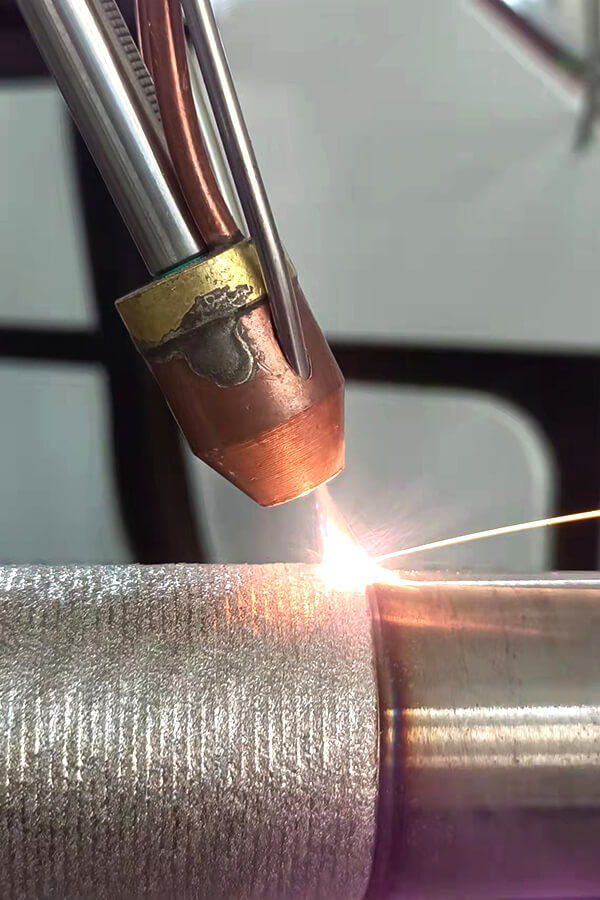
Quick Q&A – About Laser Cladding Machine
We’ve compiled a list of brief answers to common questions about the Laser Cladding Machine and laser cladding technology. If you’d like to delve deeper into these topics with us, you’re always welcome to contact Deewi Automation.
Laser Cladding Machine
As professional laser cladding equipment suppliers, Deewi Automation boasts a wealth of experience and well-established solutions. If you’re in search of a suitable Laser Cladding Machine provider, we are very eager to engage in a discussion with you.

Portable Laser Cladding Machine
Supports both manual and automated welding operations, with one-button switching between laser cladding and laser welding.
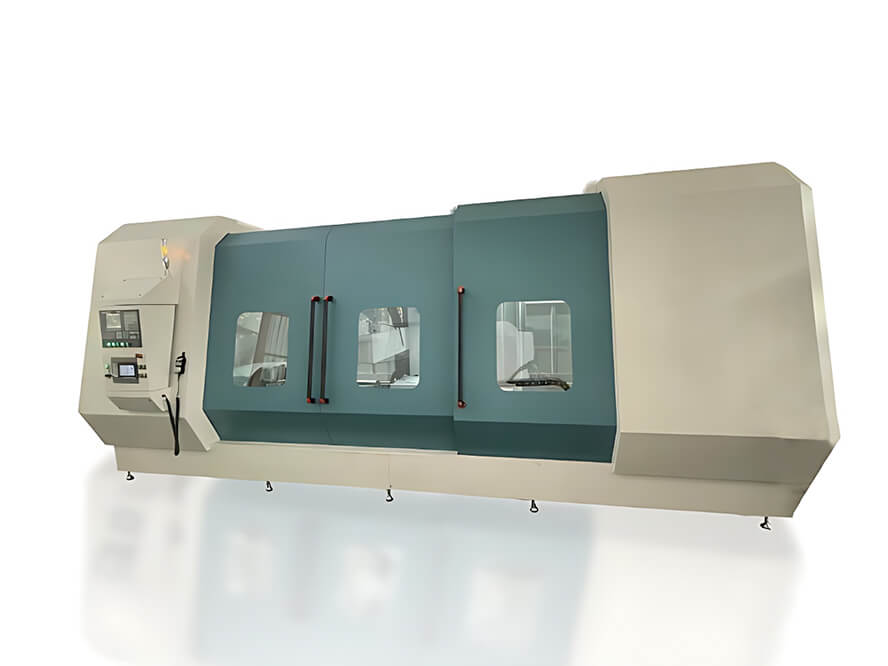
CNC High-Speed Laser Cladding Machine
Fully enclosed CNC-controlled design, with customizable internal structure. It offers high work efficiency, superior product quality, and strong versatility in equipment use.
Laser Cladding Process&Applications
We readily share knowledge related to laser cladding technology and the applications of Laser Cladding Machines. If you’re interested in what we have to offer, feel free to follow and reach out to us.
Deewi Automation Technology Co.,Ltd.
We are glad to offer technical solutions to people who are interested in our products. You just need to fill a form.
Get in touch with us today!