Worm Gears by Plasma Hardfacing
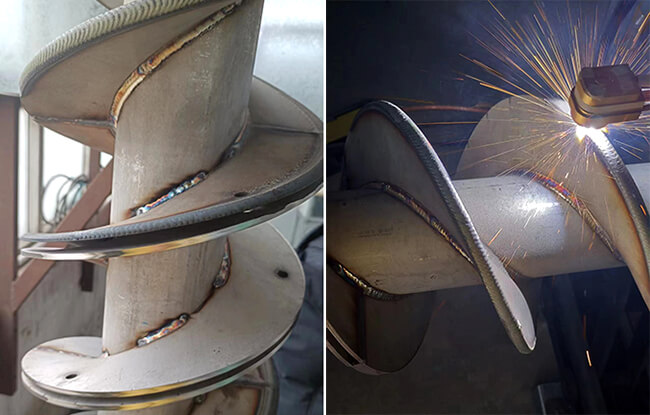
Worm gears are frequently used in industry and are commonly found in centrifuges, serving as one of the core components. Horizontal centrifuges are applied in areas such as wastewater treatment, protein separation, oil drilling, mud mixing, and food processing. For example, in wastewater treatment, they can be used to separate and extract useful components from suspensions. During routine operation, worm gears experience heavy loads and are prone to wear and damage. Their service life largely depends on the wear resistance of the helical blades on the worm gear. It has been proven that surfacing the blades with wear-resistant material at points of high wear significantly extends their lifespan.
Automated Plasma Welding Machine for Worm Gears:
To improve the lifespan of centrifuges, it is necessary to surface the helical blades and other wear-prone areas of the worm gear with a 4mm thick wear-resistant layer. Deewi Automation, catering to the special structure of worm gears, has customized a Plasma Transferred Arc (PTA) hardfacing machine. This fully automated plasma welding machine has a high degree of automation and is capable of intelligently adjusting and recognizing the distance between the welding torch and the workpiece according to the unique shape of the helical blades. In small spaces where only short-distance welding is possible, a low-current welding torch is used, while in more spacious areas, a high-current welding torch can be employed.
In terms of welding direction, the machine is not limited to horizontal welding but can also weld vertically. Typically, the outer edge surface of the spiral shaft can be welded using either horizontal or vertical methods, both of which are efficient. However, when welding the working surface of the helical blades, vertical welding is the most suitable method.
The Use Process of the Worm Gear Plasma Welding Machine:
Typically, the welding task can be completed in a few simple steps: fix the workpiece, set parameters, compile the welding program path, start welding, and remove the workpiece.
Advantages of Plasma Hardfacing Worm Gears:
- Simple to use and maintain: Typically, the worm gears do not require pre-heating or post-weld treatment, making operation and maintenance straightforward and convenient.
- Flexible and adaptable operation: The operation is simple and flexible, with good adaptability, allowing multi-angle, multi-position welding of various complex shapes to meet diverse product requirements.
- High welding precision: Thanks to the controllability and consistency of plasma welding, parameters and paths can be precisely set according to needs, ensuring high precision, quality, and stable welding.
- High welding efficiency: The use of automated welding tools significantly improves welding efficiency and consistency, reducing labor intensity and technical demands on workers.
The use of new plasma welding machines in the production and maintenance of worm gears is becoming increasingly common. Their high welding precision, flexibility, convenience, and cost-effectiveness have been widely recognized. If you are also interested in acquiring one, please contact Deewi Automation.