Laser Cladding of Cylindrical Structures – Extruder Barrels
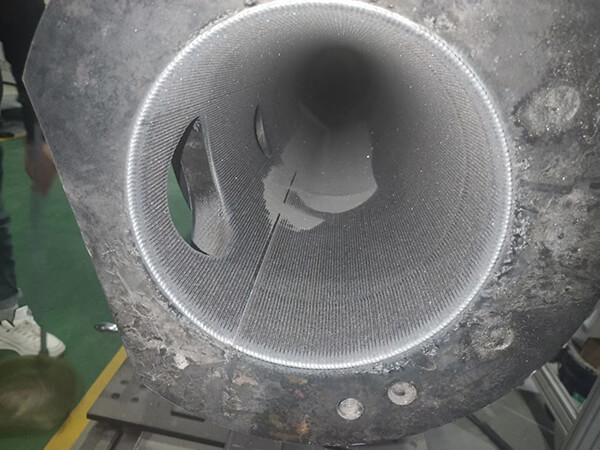
Plastic extruders are among the common machines used in the manufacturing of plastic products. Screw extruders rely on the pressure and shear force generated by the screw’s rotation to thoroughly mix and plasticize the material. The extruder barrel (also known as the feed cylinder) is a crucial component of the extruder and is typically made of alloy steel. During operation, to ensure materials are sufficiently heated and plasticized, the barrel’s length is usually 15 to 30 times its diameter. This slender structure requires adequate thickness and rigidity. Furthermore, it must withstand high temperatures, high pressures, and constant friction during operation. Therefore, it is critical for the extruder barrel, especially the inner wall, to possess excellent strength, wear resistance, heat resistance, pressure resistance, corrosion resistance, and a smooth interior.
Taking as an example a laser-clad extruder barrel with an inner diameter of 190mm and a length of 1380mm, we use a three-layer laser cladding process. The first and second layers of material are made of stainless steel powder, while the third layer is cladded with high-hardness noble metal powder material. After the laser cladding process, the inner wall hardness of the barrel reaches HRC 65-70. Additionally, the clad layer is inspected and found to be dense in structure, free of cracks and porosity defects. In practical use, the performance of the cylinder is significantly enhanced, resulting in good operational effects and a prolonged service life.