Working Principle and Applications of Laser Hardening Machines
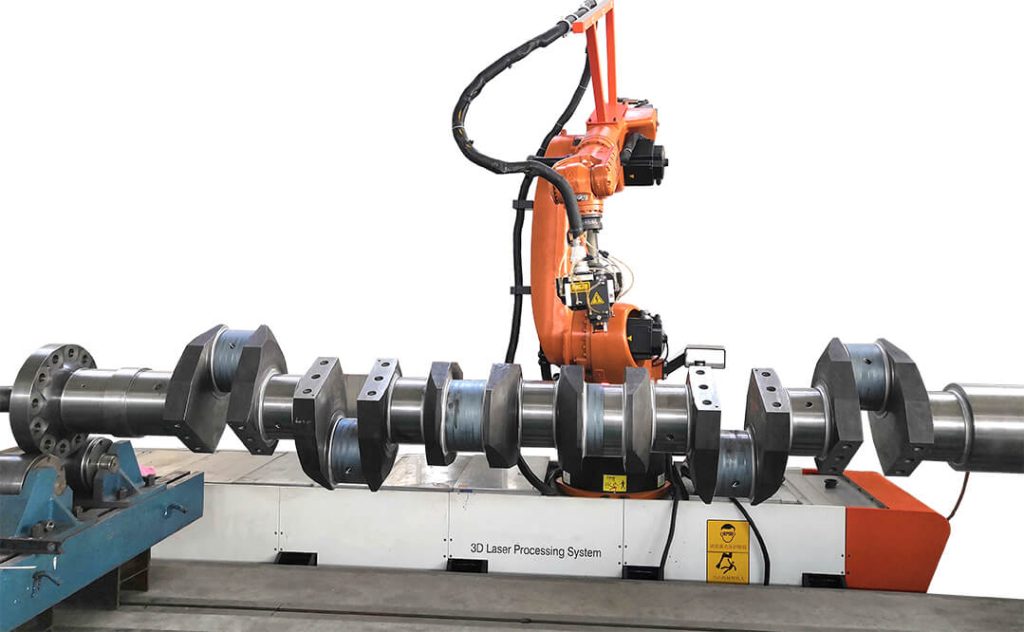
Introduction to Laser Hardening Technology:
Laser hardening technology, as an innovative technique in the modern industrial field, is increasingly recognized and used for its precision and efficiency. This technology involves high-energy laser beams pinpoint-heating metal surfaces, followed by rapid natural cooling through heat conduction, creating a “self-quenching effect” that hardens the metal surface. The heated area is precisely designed, not affecting the overall structure, dimensions, or performance of the workpiece. It significantly enhances the material’s surface hardness and wear resistance. The process is safe, controllable, efficient, and the results are precise and effective. With the continuous development of industrial automation, the application of more intelligent automatic laser hardening machines has expanded to many fields, such as automotive manufacturing, aerospace, and heavy machinery. In these industries, laser hardening technology not only improves product durability but also enhances the reliability, stability, and safety of the production process. As a low-pollution technology, laser hardening aligns with our pursuit of green, sustainable production.
Working Principle of Laser Hardening Machines:
Laser hardening machines use laser technology to spot-heat metal surfaces, improving their hardness and wear resistance. This method is primarily used for surface treatment of metal workpieces, particularly suitable for products requiring enhanced surface wear resistance without affecting the overall structure. The working process begins with the precise positioning and use of advanced lasers, such as CO2 lasers, which emit high-energy laser beams focused on the target area of the metal. During this process, the high-energy laser instantly heats the material’s surface to the phase transition temperature (typically 900°C-1300°C) but does not melt the metal. This rapid heating triggers internal structural changes in the metal, causing an austenitization reaction. Temperature control during heating is crucial; precise control of the temperature range is needed, ensuring even heating within the treated area to avoid local overheating or undercooling. Overheating can lead to material deformation, while undercooling may fail to achieve the desired hardening effect. After heating, the laser beam moves to the next area, and the material’s surface cools rapidly through internal heat conduction. This rapid heating and cooling process transforms the surface’s austenitic crystal structure into a harder martensitic structure, significantly enhancing the material’s surface hardness and wear resistance.
Main Advantages of Laser Hardening:
As an innovative metal surface treatment technology, laser hardening has unique advantages over traditional methods like flame hardening or induction hardening. These advantages not only improve processing efficiency but also enhance the quality and performance of the hardened workpieces. Common benefits of laser hardening technology include:
- Precision Control: The core advantage of laser hardening technology lies in its extremely precise control capability. Using advanced lasers and automated control systems, laser hardening can precisely control the heating temperature and area, avoiding overheating or uneven heating issues. This precision is particularly important for processing complex shapes or small components. Additionally, laser hardening technology excels in custom hardening treatments for specific workpieces.
- Reduced Deformation Risk: Since the laser hardening process is non-contact and the heating area is confined to a small region, the overall shape and dimensions of the workpiece do not significantly change due to heating. This is especially important when processing products with high dimensional precision requirements.
- Environmental Friendliness: The laser hardening process does not require additional cooling fluids, produces minimal waste, and reduces environmental pollution. The process is also efficient, with higher energy utilization, making it a more environmentally friendly treatment method.
Applications of Laser Hardening Machines in Various Industries:
Laser hardening machines are being discovered and utilized in an increasing number of industries, particularly in fields where high product performance is required, such as automotive, aerospace, and heavy machinery manufacturing.
- Automotive Industry: In the field of automotive manufacturing, laser hardening is widely used to enhance the wear resistance and durability of auto parts. This includes the treatment of critical components like gears, shafts, and drive shafts, to strengthen their fatigue resistance and extend their lifespan. Additionally, due to the precise control over the heating area, laser hardening is particularly suitable for parts with complex geometries, which are common in the automotive industry.
- Aerospace: The aerospace industry demands high material performance, and the application of laser hardening technology helps to enhance the wear resistance and corrosion resistance of key components like turbine blades and landing gear. This not only improves safety but also reduces maintenance costs and downtime.
- Heavy Machinery Manufacturing: In the field of heavy machinery manufacturing, laser hardening is often used for processing parts that are exposed to extreme wear conditions, such as excavator buckets and mining equipment cutting tools. Laser hardening effectively enhances the wear and impact resistance of these parts, thereby extending their service life and reducing maintenance needs.
Besides these industries, laser hardening machines are also widely used in agricultural machinery, mold manufacturing, medical equipment, and more. Its high precision and customizable processing characteristics make it extensively used in high-tech and high-performance demanding fields.
Market Price Overview of Laser Hardening Machines:
Understanding the market price factors of laser hardening machines is crucial for businesses to set budgets and make purchasing decisions. Several factors influence the price of laser hardening machines, including technical specifications, equipment size, manufacturing brand, and additional features.
Determining Factors of Price:
- Technical Specifications: The power and type of laser, as well as the brand, are among the main factors affecting the price of laser hardening machines. Machines using high power, high precision lasers tend to be more expensive.
- Equipment Size and Complexity: Larger machines or those with complex functionalities are more expensive. For example, machines equipped with higher precision temperature control and automation features will have a higher price tag.
- Brand and Quality: Equipment from well-known brands and manufacturers that offer quality after-sales service tends to be more expensive, but reliable after-sales service usually means higher reliability and durability of the equipment. Additionally, if the manufacturer is located in a region with a strong supply chain capability, this can significantly reduce their production costs.
Price Range:
The price range for laser hardening machines is broad. Smaller, low-power, and simply designed machines might cost a few thousand dollars, while large, high-end industrial machines may cost hundreds of thousands of dollars. However, it’s important to note that higher prices do not always directly reflect higher performance. Before discussing price, it’s advisable to consult with the equipment manufacturer based on your budget to recommend the most suitable configuration for your use.
Considerations:
When deciding to purchase a laser hardening machine, consider factors such as performance, compatibility, energy consumption, after-sales service, and maintenance costs. When budgeting for equipment, potential operational and maintenance costs are equally important, as they can significantly impact the return on investment in the long term.
How to Choose the Right Laser Hardening Machine Supplier?
Choosing the right laser hardening machine supplier is crucial for ensuring long-term stable operation, processing quality, and follow-up service of the equipment. When making a decision, the following key factors should be considered:
- Technical Expertise and Experience: First, select a supplier with extensive experience in the field of laser hardening. Suppliers with rich experience can usually provide more reliable equipment and solutions. Assessing a supplier’s industry experience requires referencing their case studies and engaging in long-term, friendly pre-sales communication.
- Product Quality and Performance: Before purchasing, evaluate the quality and performance of the laser hardening machines offered by the supplier. Especially before buying large equipment, carefully verify the specific parameters of the machine and the brand information of important components. If possible, it’s best to conduct an on-site inspection of the supplier. High-quality machines can not only improve production efficiency but also reduce long-term operational and maintenance costs.
- Customer Service and Support: Good customer service and technical support from the supplier, such as offering operation and safety training, installation, and maintenance, help in quickly mastering the operation of new machines and ensure long-term stable running. Especially in the event of equipment issues, quick and effective assistance is valuable.
- Customization Services: Customized solutions are often needed in daily applications. Therefore, suppliers who can offer customized services and flexible system configurations will help you get the machine that best meets your needs within your budget.
Cost-Effectiveness: Before purchasing, consider the overall cost-effectiveness of the machine. Not only should the purchase price be evaluated, but long-term operational and maintenance costs, as well as the machine’s production efficiency and cycle times, significantly impact the long-term investment return. - Industry Certification and Standards: Choose suppliers who comply with the certifications and standards of your region and industry, especially in areas with mandatory certifications or standards. Although this may mean higher costs, it meets regulatory requirements and ensures product quality and service.
Future Trends and Summary of Laser Hardening Machines:
As an innovative technology, laser hardening is evolving with continuous advancements in technology and processes, the use of more advanced and efficient lasers, and the development of material science. High-end laser hardening machines will become more integrated and automated. Laser hardening systems will be combined with robotics, artificial intelligence, and more advanced control systems to achieve efficient, automated, and intelligent production. While improving production efficiency, these systems will achieve higher processing precision. In the future, new laser hardening technologies will replace traditional hardening techniques in many fields. If you are interested in laser hardening technology, Want to know more about Laser Hardening machine,feel free to contact Deewi Automation.