Laser Hardening Systems
Deewi Automation: Your Premier Manufacturer, Supplier, and Exporter of High-Quality Laser Hardening Machines. Our plasma laser hardening systems represent our leadership in precision manufacturing and innovative solutions designed to meet your highest requirements for workpiece surface treatment.
Innovative technology, outstanding performance
Deewi’s plasma laser hardening system uses a high-energy-density laser beam to directly act on the metal surface, which not only significantly improves the surface hardness of the workpiece, but also effectively enhances its wear resistance and corrosion resistance. Whether you are facing complex industrial components or precision manufacturing needs, Deewi’s laser hardening systems provide unparalleled solutions.main feature:
- High efficiency: Rapid heating and cooling processes greatly increase production efficiency.
- Precise control: Utilize advanced control systems to ensure uniformity and accuracy of laser hardening processes.
- Wide adaptability: Applicable to a variety of metal materials and able to meet the needs of different industries.
- Minimized deformation: Local processing technology ensures minimal deformation of the workpiece and maintains its original shape.
- Environmental protection and energy saving: Compared with traditional hardening methods, the laser hardening process is more environmentally friendly and consumes less energy.
Application scenarios of laser hardening system
- Mold Manufacturing: Enhances mold wear resistance and hardness, extending lifespan and reducing maintenance.
- Automotive Industry: Improves surface hardness of critical parts like gears and bearings, enhancing wear resistance and fatigue life.
- Aerospace: For components operating under extreme conditions, it boosts wear and fatigue resistance.
- Heavy Machinery: Applied in construction, mining, and agricultural machinery components to increase hardness and durability.
- Metal Processing: Hardens tools such as cutters and drill bits to improve cutting efficiency.
- Medical Devices: Enhances wear and corrosion resistance of surgical tools, ensuring reliability and longevity.
- Energy Sector: Processes critical components in wind power and oil extraction, enhancing durability and reliability.
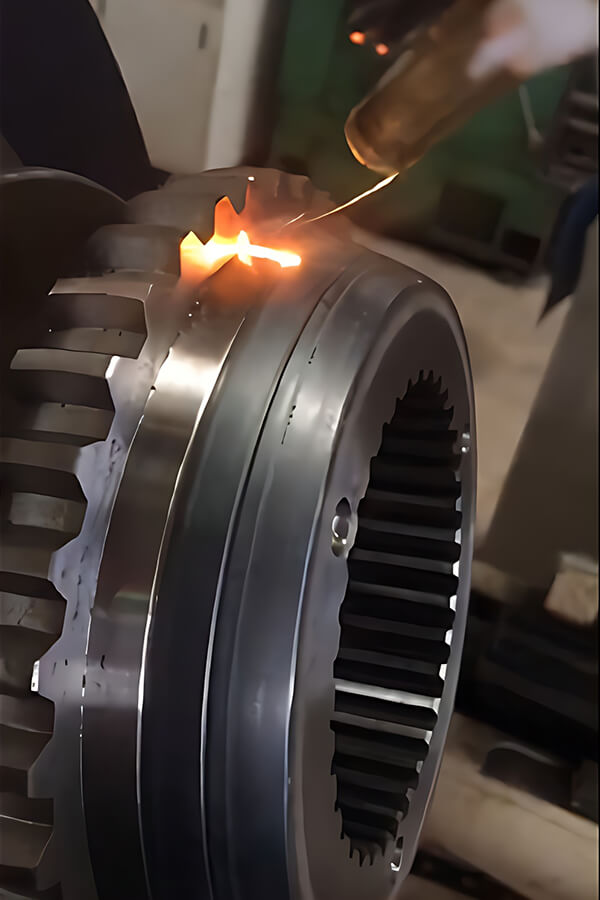
Quick Q&A – About Laser Hardening.
We’ve compiled a list of brief answers to common questions about the Laser Hardening Machine and Laser Hardening technology. If you’d like to delve deeper into these topics with us, you’re always welcome to contact Deewi Automation.
Laser Hardening Process&Applications
We readily share knowledge related to Laser Hardening technology and the applications of Laser Hardening Machines. If you’re interested in what we have to offer, feel free to follow and reach out to us.
Deewi Automation Technology Co.,Ltd.
We are glad to offer technical solutions to people who are interested in our products. You just need to fill a form.
Get in touch with us today!