Laser Hardening vs. Traditional Hardening Techniques: A Technological Revolution
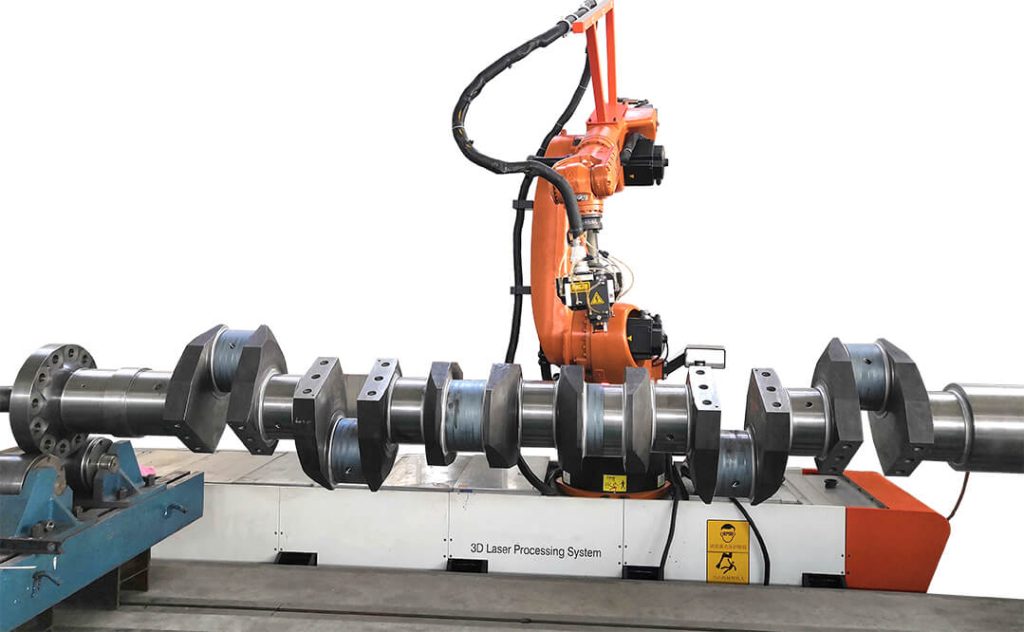
Exploring how laser surface hardening brings revolutionary changes compared to traditional hardening methods like flame hardening or induction hardening.
Basic Concepts of Laser Hardening vs. Traditional Hardening Techniques:
With rapid advancements in industrial manufacturing technology, laser hardening, as a new process, is being discovered and applied in various fields. Compared to traditional hardening methods like flame hardening or induction hardening, laser hardening offers unique advantages and innovations. It employs a high-energy laser beam to directionally heat the metal surface, quickly raising its temperature to the phase transformation point without melting the surface. The significant advantage of laser hardening is its ability to precisely control the hardening process. It improves product hardness and wear resistance while maintaining the material’s internal elasticity and toughness without adversely affecting the overall structure.
Unlike traditional hardening techniques, laser hardening doesn’t require water or other media for cooling; it relies on the material’s own “self-quenching effect.” This makes the process more flexible, safe, and environmentally friendly. It’s particularly suitable for applications needing improved localized wear resistance, such as in gears, shafts in automotive, aerospace, and heavy machinery manufacturing. With minimal environmental impact, laser hardening is a clean and rapid process, making it the preferred technology for metal surface treatment in certain industrial areas.
Overview of Traditional Hardening Methods:
Understanding the basic principles and applications of traditional hardening methods is essential before delving deeper into laser hardening technology.
Working Principles of Traditional Hardening Methods:
Traditional hardening methods like flame hardening and induction hardening have long been widely used in industrial production.
- Flame Hardening: This technique employs specialized equipment and torches to directly heat the metal with a high-temperature flame. After heating the metal to the appropriate temperature, water or other cooling media are used to rapidly cool the heated area, forming a hardened layer of martensitic structure. This method is generally suitable for steels with carbon content between 0.3% and 0.6%, effectively providing surface strengthening. However, it is challenging to precisely control the heating depth and temperature.
- Induction Hardening: This method uses alternating magnetic fields generated by induction coils to heat the metal. It can also rapidly heat the metal surface to the required hardening temperature but usually requires water for rapid cooling. Induction hardening allows for control over the heating depth and temperature and is typically used for continuous operations on production lines, particularly for batch hardening of shafts and ring-shaped parts.
These traditional hardening methods are still prevalent in industrial production, but they often face limitations compared to laser hardening. For instance, flame and induction hardening have larger heat-affected zones, potentially causing material distortion or cracking, especially when dealing with large or complex-shaped components. Additionally, these methods lack the precision, control, and flexibility of laser hardening. They are also less efficient in terms of energy usage and environmental impact.
The Principle and Process of Laser Hardening:
How does laser surface hardening work?
The basic principle of laser surface hardening relies on the thermal effects of high-energy lasers. When a laser beam is focused on the metal surface, it rapidly heats the metal’s surface layer to a phase transformation temperature. This temperature is sufficient to alter the metal’s microstructure without melting the surface. Once the laser moves away, the metal surface rapidly cools, forming a hard and stable martensitic structure, significantly enhancing the metal’s surface wear resistance. This process is often referred to as the metal’s “self-quenching phenomenon.” As the laser only affects the metal’s surface, its interior remains largely unchanged, preserving the original elasticity and toughness.
During the laser hardening process, since the laser only heats the material’s surface, the cold material beneath acts as a cooling medium. This self-quenching phenomenon promotes the formation of martensite. Compared to traditional heat treatment methods, laser hardening eliminates the need for additional cooling steps or media, such as water or oil quenching. This not only makes the operation more convenient and flexible but also enhances processing efficiency and safety.
Laser hardening typically boasts high precision and control. By adjusting parameters such as laser power, scanning speed, and focus size, the depth, area, and temperature of heating can be precisely controlled, making it particularly suitable for parts with complex shapes or where precise hardening areas are needed.
Applications and Limitations of Laser Hardening:
Laser hardening technology, as an advanced metal surface treatment method, is widely used in many industrial fields and is being adopted in more areas due to its potent capabilities. However, like any other technology, laser hardening has its specific application range and limitations.
In practical applications, laser hardening effectively improves the wear resistance and fatigue strength of components, widely used in gears, bearings, shafts, and sleeves. Traditional processes often struggle with uneven heating or dimensional distortion in these parts. Additionally, laser hardening is suitable for a variety of metals, including steel, cast iron, aluminum alloys, and titanium alloys. It is particularly effective on high-carbon steel, significantly increasing surface hardness, wear resistance, and durability while retaining elasticity and toughness in other parts of the component.
However, laser hardening has its limitations. For instance, it cannot process materials with high thermal conductivity or high reflectivity. Sometimes, to reduce reflection of the laser beam, a coating is applied to the metal surface before processing. Additionally, due to high equipment costs, laser hardening is not cost-effective for small-scale production or low-cost applications. Moreover, the need for precise design and control of process parameters demands a certain level of technical skill from operators.
In conclusion, although laser hardening offers many advantages over traditional techniques, it may not be suitable due to material characteristics, high equipment costs, and the complexity of the technology. Understanding both the strengths and limitations of this technology is crucial in choosing the right process for specific needs.
Laser Hardening vs. Traditional Hardening: A Comparative Advantage:
Unique Advantages of Laser Hardening:
In industrial production, where increasing the hardness and wear resistance of metal parts is often required, traditional hardening methods like flame hardening and induction hardening have been widely used. However, as understanding and improvements in laser hardening technology continue to evolve, it is being recognized and utilized in an increasing number of fields. So, what are the advantages of laser hardening compared to traditional hardening processes?
- Higher Precision and Better Control: Laser hardening allows for very precise control over the hardened area. We can accurately control the parameters of the hardening process, such as heating speed, temperature, and hardened layer thickness. This minimizes the impact on the workpiece, maintaining its overall dimensional stability, especially when dealing with complex or irregular shapes. This ensures effective hardening without deforming the shape.
- Higher Production Efficiency: Unlike traditional hardening techniques, which require lengthy heating and cooling, laser hardening has a high energy density and heating efficiency. It quickly heats up and then utilizes the material’s own cooling effect to rapidly cool down, forming a “self-quenching effect,” significantly reducing hardening time. This advantage is particularly suitable for automated batch production processes, significantly improving processing efficiency.
- Smaller Heat-Affected Zone in Laser Hardening: Due to the highly concentrated nature of laser heating, the heated area can be precisely controlled, resulting in the smallest heat-affected zone. This significantly reduces the overall heat input to the material, greatly reducing the possibility of material deformation. This is particularly important when dealing with workpieces that require strict dimensional accuracy.
- Wide Application Range and More Environmentally Friendly: Laser hardening technology is applicable to various complex shapes and different types of materials. It can be used on various steels and cast irons, as well as other materials like aluminum alloys and titanium alloys. The process does not require cooling media, reducing pollution and making the process more environmentally friendly.
In summary, laser hardening technology has many advantages over traditional hardening techniques in terms of precision, speed, deformation, safety, environmental protection, operational flexibility, and control. These advantages make laser hardening technology increasingly recognized and used in various fields.
As technology continues to progress, laser hardening technology will be further optimized and improved. As an innovative metal surface treatment technology, laser hardening is showing great potential in multiple industrial fields. With further technological development and cost reduction, it is expected to replace traditional processes in even more applications. Laser hardening technology also has a positive impact on reducing energy consumption and environmental pollution. With the continuous advancement and cost reduction of laser technology, its advantages will become even more apparent. If you share our views, feel free to contact Deewi Automation to discuss further.
Question 1: What is the process of laser hardening?
Answer 1: The process of laser hardening follows these basic steps: First, the workpiece (such as steel or cast iron) is placed under the laser. Then, the laser is activated to heat the surface of the workpiece to a temperature close to its melting point (usually 900-1400°C). Next, the laser moves along a predetermined path, and once the surface of the workpiece reaches the required temperature, it moves to the next area. The workpiece surface rapidly cools due to internal heat conduction, preventing carbon atoms from returning to their original lattice positions, thus forming a harder martensitic crystal structure on the surface of the workpiece.
Question 2: Does laser hardening of materials require a quenching medium?
Answer 2: During the laser hardening operation, a traditional quenching stage is usually not required. Unlike traditional heat treatment processes where workpieces need to be immersed in a liquid for quench hardening, laser-hardened workpieces form a “self-quenching effect” through their own heat conduction. Therefore, no additional cooling operations or cooling media are needed. This is one of the advantages of laser hardening, as it not only simplifies the hardening process but also reduces environmental pollution.