Materials Suitable for Laser Hardening and Their Selection Criteria
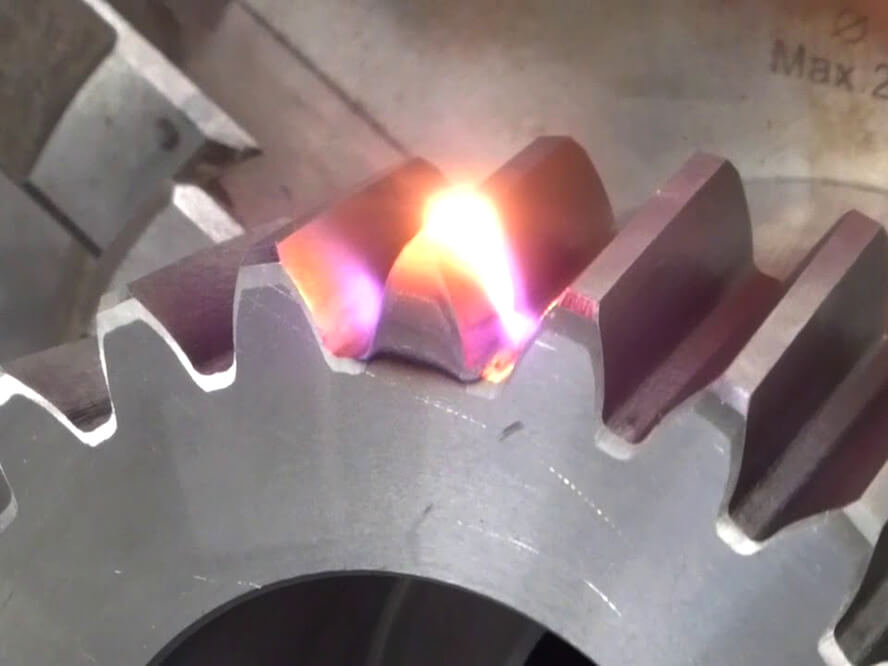
Exploring why choosing the right material is crucial in the laser hardening process and how to make such a choice.
In modern industrial production, laser hardening technology has become an important means of enhancing the wear resistance of metal parts. However, laser hardening technology has its limitations in terms of material selection. Understanding the types of materials suitable for laser hardening is essential for improving our work efficiency and product quality. Below, we discuss the material characteristics that are suitable for laser hardening technology.
Determinants for Material Selection in Laser Hardening:
Laser hardening involves using a high-energy laser beam to directionally heat the surface of a metal workpiece, resulting in austenitization. Subsequently, through the workpiece’s own heat conduction effect, it rapidly cools to form a hard and wear-resistant martensitic structure. Therefore, the carbon content, thermal conductivity, and light reflectivity of the material are crucial to the effectiveness of laser hardening.
- Carbon Content in the Material: Steel with too low carbon content (less than 0.3%) is generally unsuitable for laser hardening. Steel and cast iron with moderate carbon content, capable of forming an effective “self-quenching effect,” are very suitable for the laser hardening process. The higher the carbon content in the material, the higher the hardness that can be achieved through laser hardening.
- Reflectivity of the Material Surface: If the material surface has a high reflectivity, it can result in poor absorption of the laser, failing to heat rapidly under laser irradiation. Therefore, surfaces that are smooth or highly reflective are usually pre-treated with coatings or polishing before processing.
- Thermal Conductivity of the Material: Materials with high thermal conductivity cannot concentrate the heat generated by laser heating, thus failing to achieve effective hardening. Conversely, materials with poor thermal conductivity cannot rapidly cool down using their own heat conduction effect, so laser hardening technology has high requirements for a material’s thermal conductivity.
- Chemical Composition and Microstructure of the Material: The chemical composition and microstructure of the material also play an important role in the laser hardening process. For instance, certain alloying elements like chromium, nickel, and molybdenum can enhance the material’s hardening capability, while others might affect the laser’s absorption rate and the material’s thermal conduction.
- High Hardening Depth Required: The depth of the hardened layer in laser hardening is usually about 0.3–0.5mm. Using more powerful lasers, the depth can reach about 1mm and, in some special materials, up to 2.5mm or more. Therefore, if a deep hardening depth is required in certain industrial applications, laser hardening may not be suitable.
Examples of Materials Suitable for Laser Hardening:
- Hardenable Steels and Pearlitic Cast Iron: Materials with moderate carbon content that can effectively undergo austenitization during laser heating, and then form hard, wear-resistant martensitic structures upon rapid cooling. For example, C60 and 1.2311 type heat-treatable steel, and 1.2312 and 1.2714 type hot work tool steels, are common materials used in laser hardening.
- Other Steels: In addition to the above regular materials, high-speed steels (such as 1.3344 type) and hot work tool steels (such as 1.2343 and 1.2344 type) are also very suitable for laser hardening. Furthermore, cold work tool steels (such as 1.2320 and 1.2363 type), rust and acid-resistant steels (such as 1.4112 and 1.4034 type), and certain types of cast iron materials (such as GG25CrMo and GGG70L) also exhibit good laser hardening characteristics.
In summary, factors such as carbon content, thermal conductivity, reflectivity, chemical composition, microstructure, and tolerances of the material directly impact the effectiveness of laser hardening. Understanding how these factors influence the laser hardening process is key to achieving the best results. With continuous advancements in laser technology and the development of new materials, the application field for laser hardening will further expand. In the future, we can expect the development of more materials specifically for laser hardening to meet our needs for specific applications.