Features of the Micro-Beam Plasma Welding Machine (Advantages and Disadvantages).
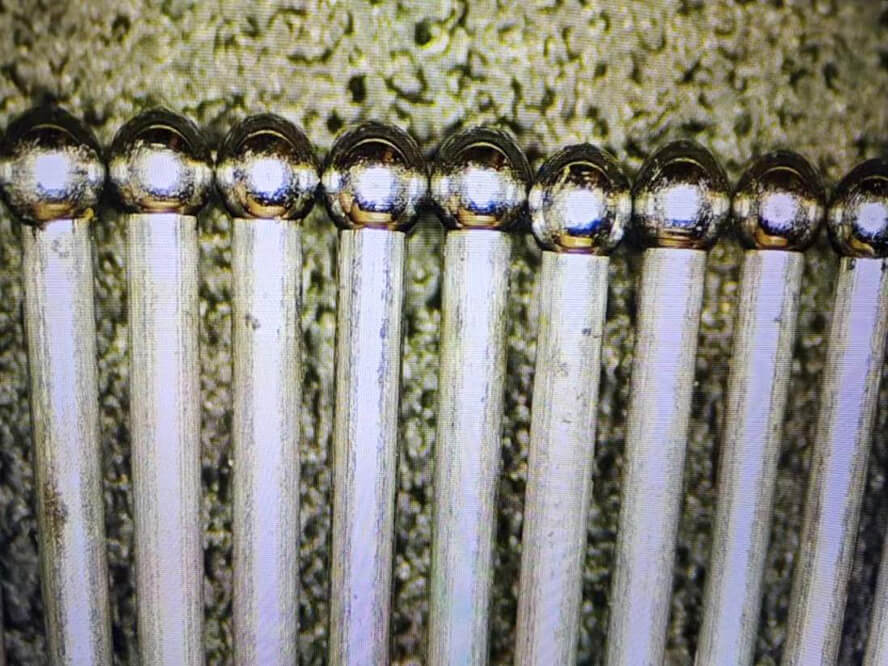
Micro-Beam Plasma Welding Machines use high-energy-density plasma arcs as their heat source. These plasma arcs are characterized by their high energy density, excellent arc stability, swift welding speed, reduced internal stress and deformation, and fine-tuned welding current control, making them ideal for precision welding tasks such as delicate thin plates or wire components. The welding features of this technology are outlined below:
- High Precision: Micro-Beam Plasma Welding Machines are renowned for their exceptional welding accuracy. They are perfect for welding components with strict tolerances or those that are minuscule and thin.
- Excellent Arc Control & Minimal Heat-Affected Zone (HAZ): The high energy density of the plasma arc results in a narrow and stable arc. Welding current, voltage, gas flow, and torch movement can all be precisely controlled. As a result, we can ensure the plasma arc affects only a tiny region, achieving accurate control over weld seam dimensions and the HAZ. This minimal HAZ, which can be controlled, significantly reduces the distortion of the component, especially when welding heat-sensitive materials. By adjusting the welding current, the energy density of the plasma arc can be controlled, allowing for reduced heat input to prevent grain growth that might affect the material’s properties and to minimize metallurgical risks. With its excellent focus and adjustable high energy density, the plasma arc can easily weld intricately shaped components, often found in aerospace, electronics, and medical equipment industries.
- Broad Applicability: The high energy density of the plasma arc allows it to weld a wide range of materials, including metals, ceramics, or other high-melting-point dissimilar materials.
- Environmental Safety: The welding process produces minimal pollution, ensuring a high-quality and clean weld.
- High Automation Potential: Micro-Beam Plasma Welding Machines can be easily integrated into automated welding systems, making them suitable for large-scale and repetitive production.
- Advanced Monitoring and Control: These machines are equipped with state-of-the-art monitoring and control systems, enabling real-time oversight of the entire welding process. This ensures a consistent and efficient welding operation and provides real-time feedback for continual process optimization.
- Versatility & Cost-Efficiency: The machines are highly versatile, and their relative cost is low.
- Complexity & Usage Limitations: Micro-Beam Plasma Welding Machines are intricate devices that consume a significant amount of gas and have substantial inter-group gaps. They also have stringent cleanliness requirements for components. Thus, they are typically suited for use in a clean indoor environment.
Given these attributes, Micro-Beam Plasma Welding Machines are especially apt for welding small, high-precision components. When welding, a power supply that offers precise control over the welding process is crucial, demanding a high-quality power source. Deewi Automation has developed a specialized DC switching power supply, adjusting wave balance, shortening the electrode’s duration, and ensuring the electrode is adequately cooled. This maintains the tip-to-tip shape, resulting in a more stable arc