How does a microbeam plasma welder generate a plasma arc?
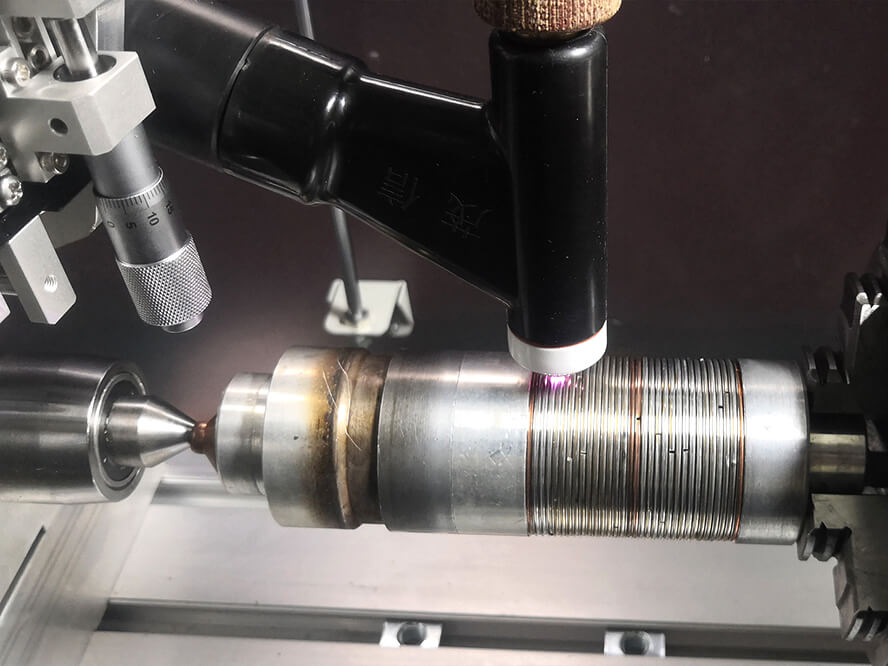
To obtain a stable plasma arc with a plasma welder, it is essential to set up and operate the machine correctly. A plasma arc is produced by ionizing the shielding gas, converting it into a conductive plasma state. When the welding current of the plasma machine is less than 30A, its arc form is typically a combined arc. This arc consists of a pilot arc (between the electrode and nozzle) and a working arc (between the electrode and workpiece). To achieve a consistent plasma arc, we must follow these guidelines:
- Proper Machine Setup:
- Ensure that the welding machine functions correctly, checking for issues such as gas or electrical leaks, and that all components are securely connected.
- The plasma arc generator (also known as a plasma torch) is crucial for producing the plasma arc. A reliable torch ensures no gas or water leaks, accurate electrode positioning, and ease of installation or replacement of components like the electrode and nozzle. Deewi Automation’s high-quality torches and accessories meet these requirements.
- The DC welding power source is a vital component influencing weld quality. Given the low welding current and high precision required for microbeam plasma welding, and the weaker ion emission capability of the arc to the gas medium, a higher no-load voltage is necessary to enhance emission effects. Deewi Automation’s power source for microbeam plasma welding is specifically designed to address these issues. Connect the welder power source in a positive manner: the tungsten electrode in the torch should be connected to the power source’s negative terminal. The positive terminal should be connected in parallel—one end to the torch nozzle through a contactor switch and the other end to the workpiece through a contactor. Always ensure power is off when checking and connecting electrical components for safety.
- Ensure all welding parameters are correctly chosen and set.
- Shielding Gas:
- The choice of shielding gas depends on the material being welded. Argon is commonly used, but mixed gases might be preferable for certain materials. Store inert gases in steel cylinders, connected to pressure regulators and flow meters to control pressure and flow. Ensure the gas flow is adequate to shield the weld and maintain a stable plasma arc. Always check for secure connections and leaks before welding.
- Initiation and Maintenance of the Plasma Arc:
- Compared to traditional welding machines, ours use high-frequency arc initiation, meaning you don’t need to touch the electrode to the workpiece to start the arc. By pressing the foot pedal or activation switch, the high-frequency mechanism and airflow are initiated, ionizing the gas and forming a pilot arc between the electrode and nozzle. Pressing the foot pedal or trigger switch again produces the main (working) arc between the electrode and workpiece.
- Move the torch at a consistent speed, maintaining a uniform arc length (distance between the torch nozzle and workpiece). Arc length directly affects the focus and intensity of the plasma arc. Stable welding speed and arc length ensure a consistent arc with uniform heat distribution and a continuous working state.
For beginners unfamiliar with a new machine, always consult the manufacturer’s instructions and operating guides. If uncertainties persist, don’t hesitate to contact your supplier. Deewi Automation offers professional round-the-clock services, including immediate information, phone, video solutions, and on-site training and guidance.