How to Improve the Welding Quality of Microbeam Plasma Welding Machines?
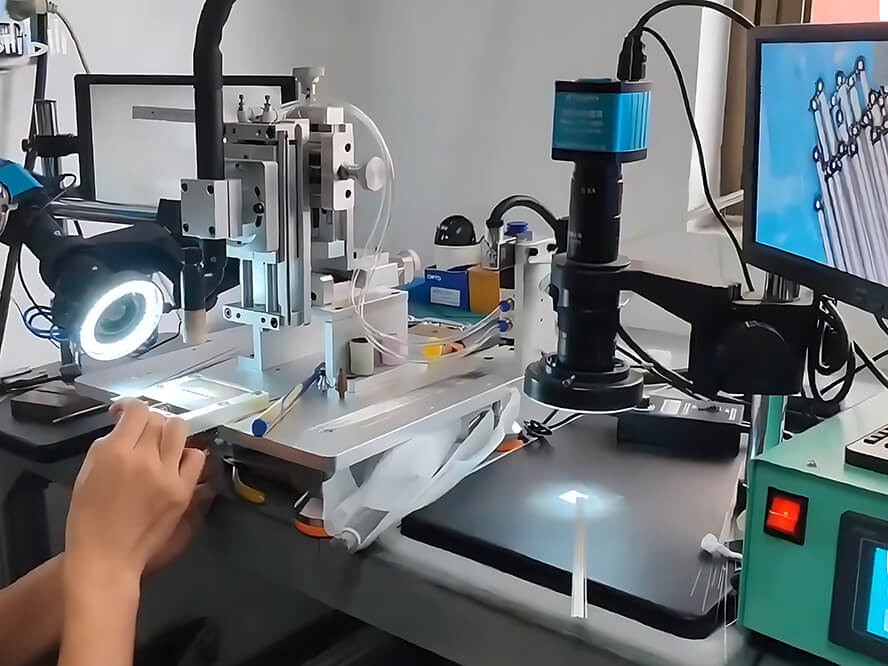
Microbeam plasma welding is a technique for joining small components, offering precise and controllable heat input for high-precision welding. The welding quality of a microbeam plasma welding machine is determined by the correct machine settings, proper pre-welding preparations, proficient welding operations, and post-weld evaluations. Here are detailed steps and considerations for enhancing the welding quality:
- Pre-weld Material Preparation:
- Ensure the workpiece and welding wire surfaces are clean and uncontaminated. Clean materials can reduce the risk of porosity in the weld.
- Select the appropriate shielding gas based on the characteristics of the welding material. Ensure a steady and sufficient gas flow. Using helium as the shielding gas often yields better welding efficiency and quality.
- For plate thicknesses over 6mm, preheat the workpiece to 100-200°C before welding.
- Ensure the workpiece is securely and precisely clamped with minimal gap and no wobble.
- Machine and Tool Inspection:
- Regularly maintain, calibrate, and ensure accurate machine parameter displays, and confirm the machine and its components are functioning properly.
- Welding Parameter Settings:
- Evaluate the welding material and requirements before welding. Set the correct welding parameters, including current, voltage, gas flow, and motion parameters. Precise parameter settings are vital for welding quality.
- Personnel Requirements:
- Operators should be trained specifically for the project or product and have relevant experience. They should be proficient in machine operation, familiar with welding parameter settings, and quality requirements. Refresh training courses based on feedback. For manual welding, the welder’s skill level is crucial, as consistent movement and speed ensure uniform and efficient welding.
- Regular safety training is essential to ensure the safety of the site and operators.
- Real-time Monitoring:
- Monitor the entire welding process in real-time. Rectify or stop welding immediately if abnormalities are detected.
- Post-weld Inspection:
- Clean and inspect the workpiece after welding to ensure quality. Periodically use tools like microscopes, X-rays, and ultrasonics to check for defects such as porosity, cracks, or incomplete fusion. Regularly conduct destructive tests like tensile or bending tests to evaluate if the weld’s mechanical properties meet requirements.
- Feedback and Summary:
- Record and feedback details for every welding session, including time, quantity, environmental temperature and humidity, workpiece batch, welding parameters, quality, issues faced, and operator. Such records help trace and rectify welding issues and optimize welding parameters and processes, ensuring consistent high-quality welding from the microbeam plasma welding machine.
In conclusion, numerous factors influence the welding quality of a microbeam plasma welding machine. Choosing experienced equipment and technical suppliers is crucial, significantly reducing your communication and trial-error costs. Deewi Automation has been deeply involved in the microbeam plasma welding field for years, boasting vast technical experience. If you’re facing challenges in this area, perhaps you should consider reaching out to us. We promise to offer you high-quality, cost-effective products and exemplary service.