How to Weld Thin Sections (Corrugated Diaphragms) with Micro-Plasma Welding Machines?
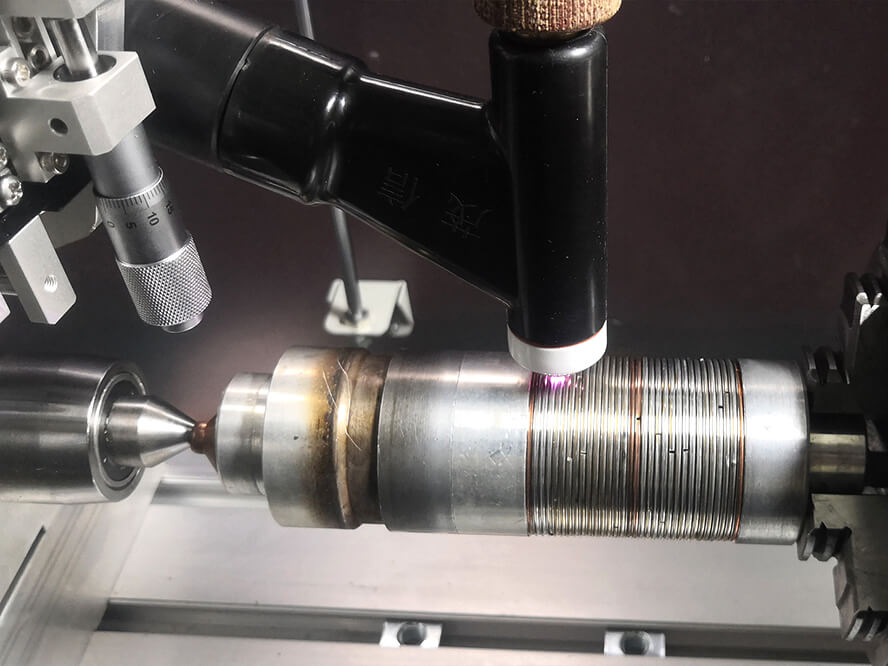
What is Micro-Plasma Welding?
Micro-plasma welding operates with smaller currents, typically less than 30A. To ensure stability of the arc at these lower currents, we generally use a compressed nozzle (0.6~1.2mm) paired with a small aperture (0.6~1.2mm). During welding, two arcs are generated: one pilot arc between the electrode and the nozzle, which initiates and maintains the arc; and a second transfer arc between the electrode and the workpiece, which melts the material. This method enhances the stability of the arc seen in conventional plasma welding, increases arc voltage endurance, reduces required welding current and air flow, allowing for a smaller arc chamber size. Thus, the plasma arc emitted from the micro-nozzle of the micro-plasma welding machine can be as fine as a sewing needle.
While its working principle is similar to TIG welding, the quality of micro-plasma welding is far superior. The plasma arc remains columnar and doesn’t extinguish when adjustments are made, leading to faster welding speeds, narrower weld seams, minimal heat-affected zones, and reduced distortion. It can weld thin metals with a minimum thickness of 0.01mm.
Why Choose Micro-Plasma Welding for Corrugated Diaphragms?
Metal bellows are generally categorized into three types: hydraulic, welded, and electroformed bellows. We refer to bellows made from corrugated metal sheets welded alternately as welded bellows. Since the Corrugated Diaphragms used to produce welded bellows are typically thin, micro-plasma welding is the preferred method. However, for sheet thicknesses greater than 0.2mm, low-power TIG welding might also be used.
How to Weld Corrugated Diaphragms using Micro-Plasma Welding?
For bellows welding, we typically employ micro-plasma welding systems. Low-power TIG welding can also be used when the Corrugated Diaphragm thickness exceeds 0.2mm. Prior to welding, the sheets must be meticulously cleaned to remove oil and oxide layers. Cleaned sheets should be soaked in anhydrous ethanol and then air-dried. During cleaning, direct contact with hands is prohibited; workers should wear lint-free gloves and use metal tongs to handle the sheets.
Once the prepared sheets are securely clamped, initiate the micro-plasma welder, strike the arc, and stabilize the plasma. Align the welding torch to the inner diameter of the Corrugated Diaphragm, maintain the arc, activate the machine’s rotational axis, and monitor arc stability and potential eccentricities. Upon verification, apply welding current, adjust welding speed, and commence welding. Once the welding parameters are correctly set and the quality meets standards, automated batch welding can begin.
While welding Corrugated Diaphragms with a micro-plasma machine, ensure that:
- The tungsten electrode is correctly aligned.
- The nozzle is cleaned regularly: Due to its small diameter, the micro-plasma welding nozzle can accumulate impurities over time, which must be removed promptly to prevent clogging and potential equipment damage.
- The workpiece is securely clamped: If clamping is inaccurate or the concentricity is off, the weld seam may appear jagged, affecting both aesthetics and sealing capabilities of the pipe.
Applications of Micro-Plasma Welding in Ultra-Thin-Walled Tubes:
Micro-plasma welders are widely used for welding and forming ultra-thin-walled tubes. We shape strip materials into cylindrical tubes and then use micro-plasma welding for joint formation. This technique is commonly employed in the production of metal flexible hoses, bellows, torsion tubes, heat exchanger tubes, and resonance tubes for instruments, among others.