Plasma Hardfacing Machine for Hydraulic Rod (Column) Repair
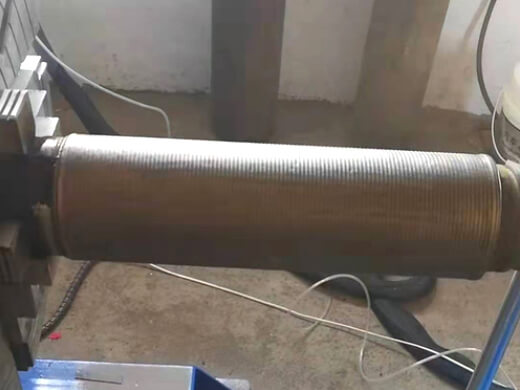
Hydraulic rods are crucial components of hydraulic supports widely used in the mining industry. Due to their operation underground, they must endure continuous exposure to various corrosive media and wear from the impact of coal and rock particles, all of which significantly affect the lifespan of the piston rods. Previously, we used electroplating to repair columns, but this method is being phased out due to its high pollution and carcinogenic nature. Plasma hardfacing repair of hydraulic rods is safe and environmentally friendly, with high precision, stronger wear layer adhesion, and improved wear and corrosion resistance.
Hydraulic Rod (Column) Plasma Hardfacing Repair Process:
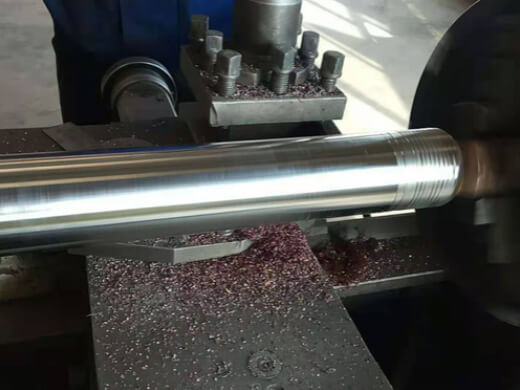
The recovery and repair of hydraulic rods (columns) involve reclaiming columns that are either scrapped or severely damaged. By using hardfacing machinery, we ensure that the repaired hydraulic or piston rods exceed the quality and performance of new products, achieving the purpose of recycling. This practice not only significantly reduces our costs but also minimizes waste of resources. The typical steps for repairing products like hydraulic rods include: surface cleaning of the workpiece → machining to grind away the worn layer → professional cleaning of the surface to be hardfaced (removing stains and chrome plating) → plasma hardfacing → dye penetrant inspection → machining of the hardfaced layer → precision grinding of the hydraulic rod surface.
Materials Used for Welding Repair of Hydraulic Rods (Columns):
For repairing hydraulic rods or piston rods, we typically use martensitic stainless steel alloy powder as the hardfacing material. This powder is produced using a water atomization method, resulting in spherical particles with a smooth surface and uniform composition. It has a melting point of 1070-1090 ℃, a flow rate of 50g/18s, and a natural density of about 4.5g/cm³. The overlay layer obtained through plasma hardfacing, after normal air cooling, consists of a martensitic structure with a small amount of austenite, with a general hardness of HRC48~HRC52. The overlay has excellent wear resistance, corrosion resistance, and tear resistance, typically achieving 3.5 times the wear capacity of the base material, and the rust prevention time in salt spray tests exceeds 120 hours.
Comparison of Plasma Hardfacing Machine and Laser Hardfacing Machine:
- Efficiency comparison: Laser cladding typically applies an alloy layer of about 0.3mm thickness per operation, whereas plasma hardfacing can apply a layer of 0.8~1mm. Thus, if a workpiece is severely worn, laser cladding is less efficient with a longer cycle.
- Cost comparison:
- Equipment cost: Based on a 1-megawatt setup, a complete laser cladding equipment set can cost up to USD 200,000.00, while plasma hardfacing equipment costs about 1/5 of that.
- Operational cost: The cost of laser cladding a hydraulic or piston rod is about USD 5/dm², compared to approximately USD 3.5/dm² for plasma hardfacing.
Of course, the above cost estimates are approximate, and actual equipment and operational costs can vary greatly depending on your specific requirements.
In the field of rods and components like columns, hydraulic rods, and piston rods, Deewi Automation has mature experience and solutions. We understand your needs and challenges, so please contact us to tailor the most suitable solution for you.