Plasma Hardfacing Process for Tunnel Boring Machine (TBM) Components.
The plasma hardfacing process is widely applied in the repair and production of tunnel boring machine (TBM) components. Here, we introduce two commonly repaired accessories:
- TBM Cutterhead Blades:
The cutterhead blade is one of the key components of a TBM. It is ring-shaped and equipped with various cutting tools, such as disc cutters or scrapers. Positioned at the front of the TBM, the cutting tools rotate to break down rock and soil as the machine advances. The annular blades are under high load during operation and need to precisely perform various cutting and crushing tasks. To ensure their long-term stable operation, regular maintenance and repairs are required. The worn parts are commonly repaired using the plasma hardfacing process to restore their functionality.
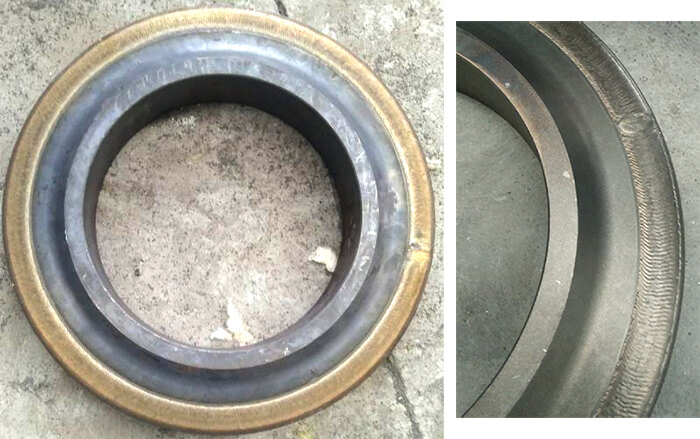
- TBM Cutter Rings:
The cutter ring, similar in shape to the cutterhead blade, is also a ring structure with uniformly distributed, raised hard alloy longitudinal ribs on its outer circumference. The cutter ring is a critical component for excavating rock tunnels, continuously crushing rock through intense pressure. Given the harsh conditions and high-load friction and compression it withstands, its surface is prone to damage. To address this, plasma hardfacing is used to weld ceramic powder, spherical tungsten carbide, or nickel-based alloy powder onto the working area surface to form a durable and stable overlay layer. Practice has shown that an overlay thickness of 2mm is optimal, significantly enhancing strength and greatly extending service life.
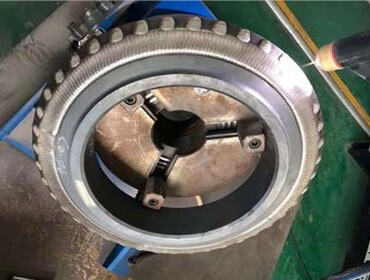
Plasma Hardfacing Machine for TBM Blades:
Repairing TBM blades with plasma hardfacing is an economical and practical process. Compared with other repair techniques, it offers lower costs, higher efficiency, and better repair quality. The hardfacing machine can be equipped with robots and a real-time monitoring system to complete repairs faster and better. It has been proven that the use of plasma hardfacing for repairs substantially reduces the frequency of replacing related components, significantly improves the overall efficiency and operating cost of the equipment, and has earned unanimous praise from customers. If you are troubled by the service life of cutting tools, you can discuss with Deewi Automation to seek the best solution.