Plasma Transferred Arc Hardfacing: Application in Blast Furnace Tuyere Copper Nozzles.
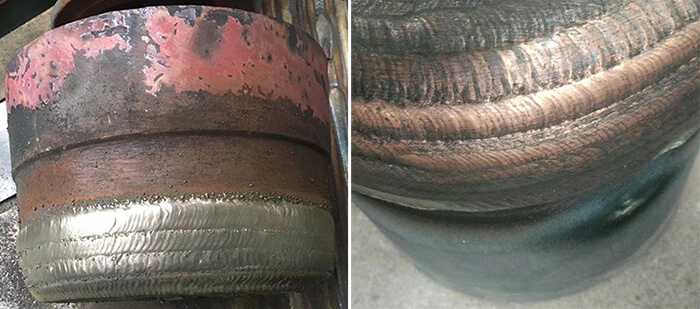
Blast furnaces are very common industrial equipment in steel and ironmaking plants. The tuyeres of these furnaces blow in high-temperature hot air rich in CO, which reduces iron oxide to iron at high temperatures. Typically installed in the furnace walls between the bosh and the hearth, the front end of the tuyere extends into the furnace, directly withstanding the thermal erosion and wear from liquid slag and iron. Frequent replacement of tuyeres can lead to furnace downtime and reduced output. Therefore, it is essential that blast furnace tuyeres have characteristics such as good thermal conductivity, uniform cooling, high cooling efficiency, compact structure, good wear resistance, and long service life. The material for blast furnace tuyeres is usually high-purity copper, with the size and shape designed according to actual usage. Copper has a high melting point and is not suitable for conventional welding processes. The high temperature of plasma arc heating makes it suitable for weld overlay at the front end of the copper nozzles of the blast furnace tuyeres.
Using plasma transferred arc cladding technology for the production and repair of blast furnace tuyere copper nozzles results in a dense and uniform cladding layer that is firmly bonded to the nozzle. This significantly improves the heat and wear resistance of the nozzles, extending their service life and reducing the frequency of replacing tuyere nozzles, thereby enhancing the safety and efficiency of production.
If your equipment is subjected to harsh working conditions and requires an overload of wear and heat resistance, you can contact Deewi Automation. We provide professional solutions to reduce the maintenance and operating costs of your equipment and improve your production efficiency, ensuring your competitive edge in the industry.