What is Arc Spray?
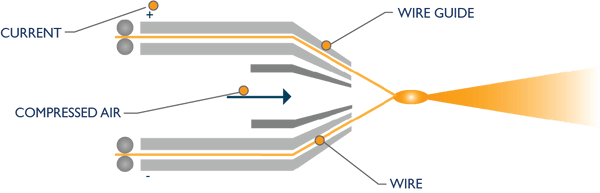
Arc spray is a process that utilizes two continuous-feed metal wires as electrodes. An electric arc melts these wires, and the molten metal is atomized by high-speed airflow and sprayed onto the substrate surface to form a coating. The two metal wires used as coating material can be of the same or different materials. This system can feed two different metal wire materials into the spray gun, creating specialized composite coatings. An arc spraying system typically consists of a dedicated power supply, control device, arc spray gun, wire feeder, and compressed air supply unit.
Operating Cost | Economical |
Bond Mechanism | Mechanical (1,500-9,000 psi) |
Max Flame Temperature | Up to 7,000° F |
Particle Velocity | 160-300 ft/sec |
Max Spray Rate | 10+ lbs/hr/100 amps |
Coating Thickness Range | 0.005″ to 0.250″ |
Special Features | Economical, no heat distortion |
Wear Resistance | Average |
Corrosion Resistance | Acceptable |
Porosity | Medium |
Arc spraying boasts several advantages:
- High Bond Strength: Arc-sprayed coatings exhibit high bond strength without elevating the workpiece surface temperature or requiring expensive metals as the base layer material.
- High Production Efficiency: The production efficiency of arc spraying is directly proportional to the spraying current. Increasing the working current enhances equipment efficiency.
- High Energy Utilization: Arc spraying demonstrates higher energy utilization rates compared to common spray methods, highlighting its energy-saving capabilities.
- High Safety: Arc spraying generally employs only electricity and compressed air, eliminating the use of flammable gases, ensuring high safety standards.
Arc spraying finds extensive applications, especially in steel structural engineering (such as bridges, high-voltage towers, steel gates, steel facilities in chemical plants, large containers in ports, and ship hulls), where it is the most commonly used method for wear resistance and corrosion prevention. In industrial contexts, it is used for repairing crankshafts, axles, printing press rollers, guide rollers, molds, capacitors, electronic products, and more.