What is Cold Spraying?
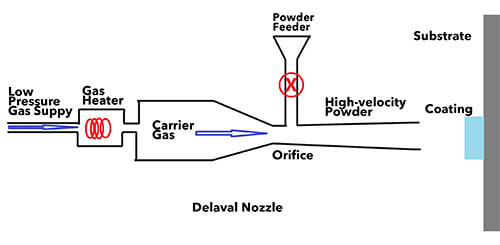
Cold spray, also known as Cold Gas Dynamic Spray (CGDS) or HVPC, represents an innovative thermal spraying technique. It employs high-pressure gas to carry powder material injected axially into a laval nozzle. Accelerated by the spray gun, the powder material impacts the substrate at supersonic speeds (300~1200m/s) over a short spraying distance (5~50mm/s) in an unmelted state, undergoing plastic deformation and depositing onto the substrate surface to form a dense coating. Cold spray operates at low temperatures, avoiding oxidation and decomposition of the substrate and coating material during spraying. It can apply materials to the substrate surface without altering their internal structure, preserving the original properties. Therefore, it is particularly suitable for temperature-sensitive materials (such as nano-phase materials and amorphous materials), oxygen-sensitive materials (such as copper and titanium), or phase-change-sensitive materials (such as carbides). Cold spray technology provides a crucial method for preparing high-performance non-oxidized coatings, nanostructured coatings, and nanoization of metal surfaces. It stands as a significant technique in surface protection, complementing and extending thermal spraying technologies.
Key Features of Cold Spray Technology:
- Low Spraying Temperature: Minimal impact on material structure and low thermal influence on the substrate. It allows the application of organic coatings, and the resulting metal coatings are practically oxidation-free.
- High Spraying Efficiency: High efficiency with the ability to recycle sprayed powder, ensuring high material utilization rates.
- Dense Coating with Low Porosity: Cold spray coatings exhibit low porosity, high density, and low residual stress.
- Ability to Prepare Various Functional Coatings: Cold spray can prepare coatings with high thermal conductivity (such as Cu, Al) and other functional coatings.
- Versatility in Substrate Selection: Cold spray can form coatings on various substrates, including metals, ceramics, or glass. Research indicates that Cold Spray can apply metals and alloys such as Zn, Cu, Ni, Al, Ag, Ti, and Ti-Ni on surfaces like PTC, glass, aluminum, and steel. The range of applicable coating materials includes most metals, metal-ceramic materials, organic materials, and more.
- Low Interlayer Stress: Cold spray coatings exhibit low interlayer stress, mainly compressive, allowing the production of thick coatings.
- Ability to Create Composite or Alloy Coatings: Enables the creation of composite coatings or alloy coatings using dissimilar materials.
- Low Noise Level during Spraying.
Cold Gas Dynamic Spray employs unique spraying methods distinct from conventional thermal spraying techniques. Ongoing research is exploring its use not only for wear-resistant and corrosion-resistant coatings but also for producing new resilient coatings for automobiles and aircraft. It is being employed in gradient coatings, connecting dissimilar metals, manufacturing small-sized composite coatings, and low-temperature coatings. Cold spray technology plays a pivotal role in expanding the field of thermal spraying, offering innovative avenues in surface protection engineering applications.