What is High-Velocity Oxygen Fuel Spray?
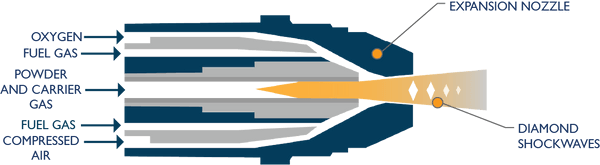
High-Velocity Oxygen Fuel spray (HVOF) is a process that utilizes a combustible gas mixture, such as H2, C3H3, or C3H6, along with high-pressure O2, or liquid fuels like kerosene and alcohol, ignited within a specialized combustion chamber or nozzle. This controlled ignition generates a high-temperature, high-speed flame that, when constrained by the nozzle, forms a supersonic, high-temperature flame flow. The flame flow can reach speeds of up to 1500-2000m/s. Powdered coating materials are introduced into the flame flow either axially or laterally using nitrogen. Due to the high velocity and temperature of the flame flow, the sprayed particles are accelerated to speeds as high as 300-650m/s, resulting in coatings with high adhesion, excellent density, minimal porosity, and low roughness after processing. The coatings exhibit low oxidation and decarburization, leading to increased hardness. Despite the high velocity, the flame flow temperature remains relatively low, effectively inhibiting WC decomposition during spraying. This characteristic ensures coatings with high bond strength, density, and superior wear resistance, comparable to Plasma Spray and Detonation Spraying. Additionally, HVOF coatings are smooth, allowing for thicknesses exceeding 1/2”.
Operating Cost | Premium |
Bond Mechanism | Mechanical (>10,000 psi) |
Max Flame Temperature | 5,600° F |
Particle Velocity | 2,000-3,000 ft/sec |
Max Spray Rate | 30 lbs/hr |
Coating Thickness Range | 0.003″ to 0.030″ |
Special Features | Capable of high corrosion and wear resistant coatings, no heat distortion |
Wear Resistance | Excellent |
Corrosion Resistance | Very Good |
Porosity | Very Low |
HVOF finds extensive applications in various sectors, particularly in industries such as mechanical engineering, power generation, metallurgy, aviation, and petrochemicals.
- Metallurgical Industry: Numerous rollers and conveyor rolls in the metallurgical industry require wear-resistant reinforcement or repair, eliminating nodules on the roll surface. Supersonic sprayed NiCr-Cr3C2 coatings offer high-temperature oxidation resistance, thermal shock resistance, and abrasion resistance, allowing furnace bottom rods to work continuously at high temperatures for extended periods, enduring periodic thermal shocks.
- Paper and Printing Industry: WC coatings prepared by supersonic spraying for calender rolls outperform cold hard cast iron in terms of wear resistance. WC coatings are particularly suitable for manufacturing large calender rolls, devoid of the casting defects associated with cold hard cast iron. Moreover, these coatings can be sprayed on the surface of dewatering box panels, with a 0.15mm-thick coating exhibiting wear resistance several times greater than stainless steel.
- Petroleum Industry: Machinery such as pumps, valves, drilling equipment, transportation devices, lifting equipment, and pipelines endure prolonged wear and corrosion. HVOF proves beneficial for enhancing and repairing pump piston rods. When coated with WC, these rods exhibit significantly improved wear resistance and increased lifespan. The technology is also widely applied in valve seats and various shaft components.
- Hydraulic and Pneumatic Equipment: Pumps, cylinders, and valves are fundamental components of hydraulic and pneumatic systems. Wear and corrosion are critical factors affecting their lifespan. HVOF strengthens and repairs components such as pump shafts, cylinder piston rods, and valve cores. These parts require high precision and low surface roughness. Supersonic sprayed coatings maintain high precision and surface quality after grinding, meeting the required standards. Moreover, hard-sealed ball valves are extensively used in industries relying on hard-seal technology. By spraying a corrosion-resistant ceramic metal coating with specific thickness on the valve core, its sealing performance and lifespan are significantly improved.
- Power Industry: Fans, impellers, boilers, and steam turbine generators are vital equipment in thermal power plants. Due to harsh working environments, some equipment has a relatively short lifespan. Coatings can extend their usage life significantly. Coal powder is transported via powder feeders in thermal power equipment. The blades of these feeders endure severe wear and erosion from high-speed coal powder. Strengthening measures for these blades include methods like flame spraying, hardfacing, embedding ceramic pieces, and supersonic flame spraying.
- Wire Drawing Equipment: Components like wire drawing tower pulleys, wire collecting reels, wire drawing cylinders, and guide grooves are critical components of wire drawing machines. Wear is the primary cause of their failure. For instance, supersonic sprayed WC coatings significantly enhance the surface of wire drawing pulleys, substantially extending their service life.
Currently, in the field of thermal spraying, extensive research is underway to replace chrome plating with supersonic spraying technology. Due to the severe environmental pollution caused by chrome plating, there is increasing pressure to explore alternative technologies. Studies have indicated that the performance of coatings produced by supersonic spraying, including adhesion, coating strength, achievable coating thickness, wear resistance, and corrosion resistance, surpasses that of hard chrome layers. Moreover, supersonic spraying offers better value for money, making it the preferred technology for replacing hard chrome plating.