What is Plasma Spray Systems?
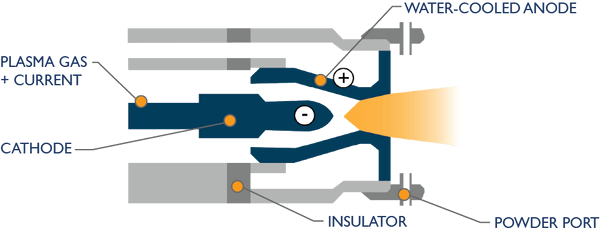
Plasma spray utilizes a direct current-driven plasma arc as the heat source, melting and accelerating ceramic, metal, or alloy coating materials onto the surface of workpieces, forming a protective layer. This process harnesses a compressed plasma arc, characterized by its fine arc column, high current density, and elevated gas ionization compared to regular arcs. Plasma spray amalgamates the features of flame and arc spraying, generating sufficiently high temperatures to effectively apply high-melting-point materials such as carbides and ceramics.
Key Characteristics of Plasma Spray Technology:
- High Flame Temperature: Allows for the melting of high-hardness, high-melting-point coating materials, ensuring strong adhesion of coatings.
- High Spray Material Jetting Speed: Results in dense, smooth, and strongly adhering coatings due to rapid melting and solidification on the substrate surface.
- Low Susceptibility to Oxidation: Inert gases are used as protective gases during spraying, preventing oxidation of the sprayed surface and minimizing impurities within the coating.
- Cost-Effective Spraying: Plasma spray system maintenance costs are low, and the equipment offers high adjustability.
Operating Cost | Upgraded |
Bond Mechanism | Mechanical (<10,000 psi) |
Max Flame Temperature | 12,000-35,500° F |
Particle Velocity | 1,500-2,600 ft/sec |
Max Spray Rate | 18 lbs/hr |
Coating Thickness Range | 0.003″ to 0.030″ |
Special Features | Capable of ceramic coating, no heat distortion |
Wear Resistance | Excellent |
Corrosion Resistance | Very Good |
Porosity | Low |
Primary Factors Affecting Plasma Spray Quality:
- Plasma Gas Composition: Choice of plasma gas is based on availability and cost-effectiveness. Nitrogen, with its affordability and high enthalpy, facilitates rapid powder melting. However, materials prone to nitridation cannot be used. Argon, although stable, has a shorter burning time, making it suitable for smaller or thinner parts but is comparatively expensive due to its inert nature.
- Gas Flow Rate: Directly influences plasma arc flame enthalpy and velocity, impacting coating efficiency and quality. Excessive gas flow speeds up plasma jetting, potentially preventing proper melting, while insufficient flow can lead to material overheating and inefficient coating.
- Arc Power: Excessive arc power increases plasma temperature and density, affecting material efficiency. Too low power reduces plasma temperature, weakening coating adhesion and deposition efficiency.
- Powder Feeding Rate: Should match input power. Excessive feeding may prevent timely powder melting, while low feeding rates cause material oxidation and substrate overheating, leading to thermal damage.
- Spraying Distance and Angle: Large distances reduce particle velocity and temperature, affecting coating quality. Short distances may overheat the substrate or cause insufficient material melting. Spray angle influences coating-substrate adhesion; angles below 45 degrees may create voids and loose structures.
- Relative Speed Between Substrate and Gun: Maintaining consistent speeds prevents uneven spraying. Overlapping each stroke ensures complete coverage without under-spraying or over-spraying areas.
- Substrate Temperature: Preheating the substrate to a specific temperature reduces thermal differences between the substrate and coating material, enhancing adhesion and overall spray quality.
Components of Plasma Spray Systems:
- Spray Gun: The heart of the system, integrating the non-transfer plasma arc generator, gas supply, coating material feeder, and cooling apparatus.
- Specialized DC Power Supply: Supplies power to the spray gun.
- Powder Feeder: Stores and transports coating powder, feeding it to the spray gun.
- Heat Exchanger: Cools the spray gun, prolonging nozzle life.
- Gas Supply System: Provides protective and feed-gas supply to the spray gun.
- Control System: Regulates and controls water, electricity, gas, and powder flow for stable and intelligent spraying, ensuring consistent, high-quality results.
With ongoing advancements in plasma spray technology and coating materials, its applications have expanded into diverse sectors, including aerospace, steel manufacturing, automotive, petrochemicals, textile machinery, and shipbuilding.