Enhancing Ball Valve Performance: Practical Applications of Laser Cladding with High-Hardness Alloys
Deewi Automation has adopted innovative laser cladding technology to enhance ball valve performance. By applying high-hardness alloy layers to the surface of ball valves, this technique significantly improves their durability, stability, and overall performance.
- Importance of Ball Valve Performance
- Overview of Laser Cladding Technology
- Advantages of Deewi Automation’s Laser Cladding Technology
- Benefits of High-Hardness Alloy Layers in Laser Cladding
- Practical Applications of Laser Cladding with High-Hardness Alloys
- Real-World Performance Enhancements
- Development Trends in Laser Cladding Technology
Importance of Ball Valve Performance
Ball valves are critical industrial components used in petroleum, chemical, natural gas, and water treatment sectors. Frequent operations and harsh environments can lead to wear and corrosion, affecting their performance and lifespan. To address these challenges, laser cladding with high-hardness alloys has emerged as a reliable solution, providing enhanced durability and reliability for ball valves.
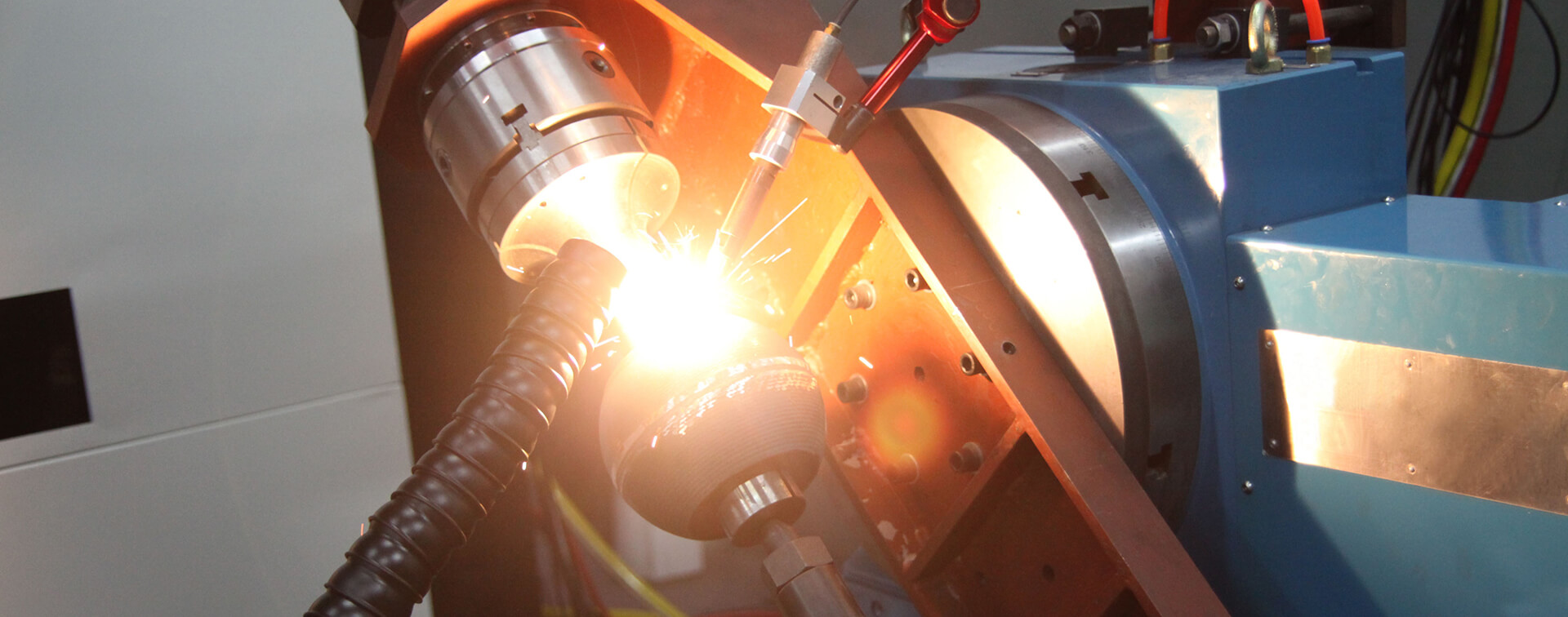
Overview of Laser Cladding Technology
Laser cladding is a technique that uses a high-energy laser beam to melt alloy materials, precisely depositing them onto the substrate surface. Known for its high precision, efficiency, and minimal thermal impact on the substrate, laser cladding has become an essential method for improving industrial components’ performance.
Advantages of Deewi Automation’s Laser Cladding Technology
- High Energy Density: The laser beam’s high energy density allows for rapid material melting, increasing cladding efficiency.
- Precise Control: The laser cladding process ensures precise control, guaranteeing uniform and consistent cladding layers.
- Material Compatibility: Suitable for various materials, including stainless steel and alloy steel, expanding its application range.
- Eco-Friendly and Energy-Efficient: Compared to traditional welding techniques, laser cladding is more environmentally friendly and consumes less energy.
Benefits of High-Hardness Alloy Layers in Laser Cladding
- Enhanced Wear Resistance: High-hardness alloy layers effectively resist wear, extending the ball valve’s service life.
- Improved Corrosion Resistance: The alloy layer offers excellent corrosion resistance against various chemical media, making it suitable for harsh environments.
- Better Sealing Performance: Laser cladding ensures smooth and precise sealing surfaces on ball valves, enhancing sealing reliability.
Practical Applications of Laser Cladding with High-Hardness Alloys
Deewi Automation incorporates laser cladding technology in ball valve production, achieving comprehensive performance enhancements by precisely controlling the alloy layer’s thickness and composition.
- Material Selection: Choosing suitable high-hardness alloy materials for cladding based on the application environment and working conditions.
- Process Optimization: Continuous testing and optimization to determine the best laser parameters and cladding processes, ensuring perfect alloy layer bonding with the substrate.
- Quality Control: Implementing rigorous quality inspection procedures to ensure each laser-cladded ball valve meets high-performance standards.
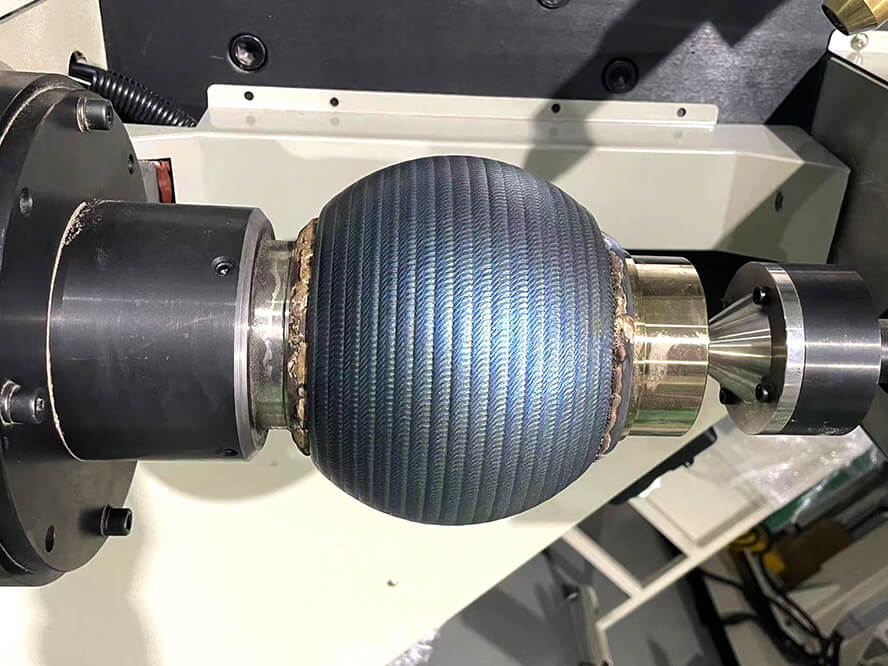
Real-World Performance Enhancements
- Reduced Maintenance Costs: Enhanced durability of ball valves reduces replacement frequency and maintenance costs.
- Increased Production Efficiency: Improved stability and reliability of ball valves decrease production line downtime, boosting production efficiency.
- Extended Equipment Lifespan: Long-lasting laser-cladded ball valves reduce the frequency of equipment replacements, lowering long-term operational costs.
Development Trends in Laser Cladding Technology
As industrial technology advances and production demands grow, laser cladding technology‘s application in plug valves will expand. Key development trends include:
- Material Innovation: Developing new wear-resistant, high-temperature-resistant, and corrosion-resistant materials to meet more stringent industrial requirements.
- Process Optimization: Refining laser cladding parameters, such as laser power, scanning speed, and powder feeding rate, to improve coating quality and production efficiency.
- Automation Integration: Incorporating robotics and automated equipment to achieve fully automated laser cladding production for plug valves, reducing labor costs and increasing production efficiency.
- Intelligent Monitoring: Using sensors and data analysis to monitor the cladding layer quality in real-time during production, ensuring product consistency and reliability.
Through the practical application of laser cladding with high-hardness alloys, Deewi Automation has successfully enhanced ball valve performance, achieving high wear resistance, corrosion resistance, and sealing performance. This innovative technology not only boosts product competitiveness but also provides an efficient and eco-friendly solution for the industrial manufacturing sector. As the technology matures and its application scope widens, laser cladding is expected to play a more significant role in driving industrial manufacturing toward greater efficiency and sustainability.