Understanding the Manufacturing of Guide Wires: An Overview
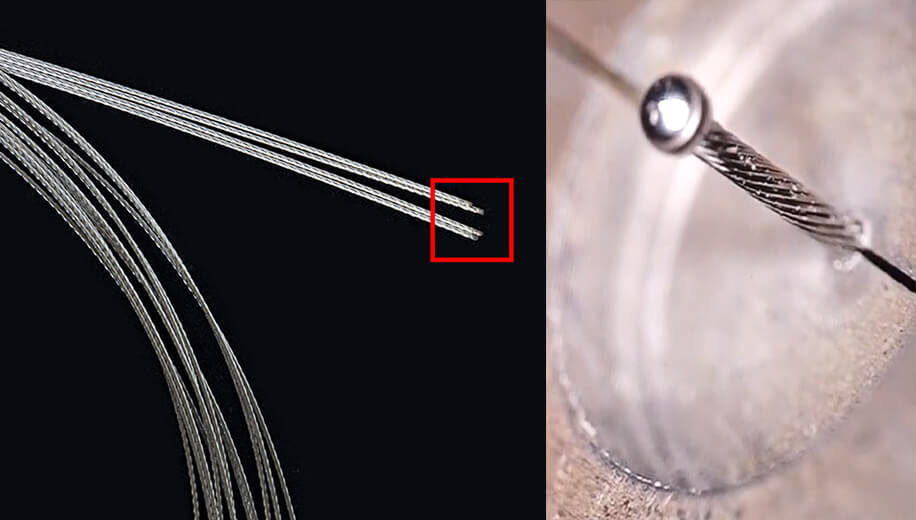
Guide wires, particularly those used in medical procedures, are precision components whose manufacturing is a highly precise and technologically driven process. Here’s some fundamental information about the manufacturing of guide wires:
- Material Selection: The core of a guide wire is typically a metal wire, meticulously controlled for diameter and strength. Given the fine diameter required for medical guide wires, which navigate through human blood vessels for complex surgeries, the comprehensive performance requirements are high. Stainless steel or Nitinol (Nickel-Titanium alloy) are commonly chosen for their strength, flexibility, and biocompatibility, making them ideal materials for medical guide wires.
- Coating: Guide wires are usually coated with substances that reduce friction, like silicone oil, PTFE (Polytetrafluoroethylene), or hydroxyapatite, facilitating smooth movement through blood vessels or other channels.
- Tip Design: The tip design is crucial for the guide wire’s performance. Depending on their intended use, guide wire tips can vary in shape – straight, J-shaped, or spherical. Tip size and length are tailored to specific requirements, and the tip material might differ from the main body to add functionality, such as visibility aids.
- Tip Processing: Tip processing is a critical step to realize the design goals and may involve cutting, welding, grinding, or forming. For instance, spherical tips on some wires are created using micro plasma welding technology. Laser welding and cutting processes are also frequently employed in guide wire manufacturing. Post-welding, the tips might require polishing and fine finishing to ensure smoothness and safety.
- Quality Inspection: After structural manufacturing, guide wires undergo various tests to ensure compliance with design specifications:
- Dimensional Accuracy: Checking the diameter and length against stringent tolerances.
- Mechanical Testing: Assessing strength, flexibility, bendability, torsional properties, and push transmission to ensure design requirements are met.
- Biocompatibility Testing: Ensuring materials and coatings are safe and harmless to the human body.
The manufacturing of guide wires is a complex process that demands high-precision techniques, specialized material knowledge, and stringent quality control. The goal is to ensure guide wires can safely and effectively navigate medical devices to targeted locations within the body. Deewi Automation specializes in the field of micro welding for guide wires, offering high-value micro welding machines. If you’re interested in these areas, please contact Deewi Automation for further information.
In summary, using micro plasma welding machines for spherical tip forming offers numerous advantages, such as high precision, excellent shaping, strong controllability, automation, and high production efficiency, making it an ideal choice for manufacturing miniature medical devices and precision components. If you are interested in learning more about “micro plasma welding technology” or “guidewire tip forming,” feel free to contact us at Deewi Automation for professional advice and discussion on your queries.
Key Questions and Answers About Guide Wire Manufacturing
Here’s a summary of frequently asked questions about guide wire manufacturing, providing insight into this intricate process:
Question 1: What impact does the design of a guide wire’s tip have on its performance?
Answer 1: The design of a guide wire’s tip, such as straight, J-shaped, or spherical, significantly influences its maneuverability and safety within the body. Different tip designs cater to varied clinical applications, impacting the guide wire’s efficacy in specific medical procedures.
Question 2: How is the quality and safety of guide wires ensured?
Answer 2: Precision in the manufacturing process, stringent material selection, and comprehensive quality testing are key to ensuring the quality and safety of guide wires. These steps verify the guide wire’s performance and compatibility with medical use.
Question 3: What are the technical challenges in guide wire manufacturing?
Answer 3: Major technical challenges in guide wire manufacturing include maintaining high precision and consistency. Ensuring consistent welding quality and precision across various welding materials and applications in mass production is crucial.
Question 4: What are the future trends in guide wire manufacturing?
Answer 4: Future trends in guide wire manufacturing involve the development and use of more advanced materials with enhanced overall performance and biocompatibility. Also, advanced manufacturing techniques and processes are being adopted, along with improvements in production through digitalization and automation, enhancing efficiency.
Question 5: What drives the increasing demand for guide wires?
Answer 5: The growing demand for guide wires is fueled by advancements in medical technology and the widespread adoption of minimally invasive surgeries and diagnostics. There’s also a growing need for customization to meet specific clinical requirements, demanding more flexible design and manufacturing capabilities.
Question 6: How is the balance between strength and flexibility achieved in guide wire manufacturing?
Answer 6: Balancing strength and flexibility in thin guide wires is paramount. This balance is achieved through the selection of appropriate materials and precise process control. For instance, Nitinol guide wires offer excellent elasticity and shape memory, while stainless steel provides higher strength and rigidity.
Question 7: How are digitalization and automation impacting guide wire manufacturing?
Answer 7: Digitalization and automation enhance the precision and efficiency of guide wire manufacturing, reducing human errors and allowing for finer process control to improve welding accuracy and consistency. These technologies also increase scalability and flexibility in production, enabling more adaptive manufacturing approaches.