Plasma Hardfacing for Valve and Gate Welding.
Why do Valves and Gates require cladding or hardfacing?
Valves and gates are ubiquitously applied in the industrial sector and our daily lives, making them virtually omnipresent. However, different valves are employed in varied scenarios, and the performance demands can vary dramatically. These requirements range from high-temperature resistance, high-pressure tolerance, corrosion resistance, wear resistance, to excellent sealing properties, among others. These diverse needs place advanced demands on the materials used for valves. Consequently, the valve industry continuously sees the emergence of innovative technologies, new materials, and state-of-the-art processes. Applying hardfacing or weld overlay cladding of wear-resistant layers on surfaces of valves prone to wear has been proven to be an effective and economical solution. Furthermore, this technique can also be employed to repair damaged components. Relying on welding-based cladding processes is a viable method for restoring performance, extending service life, reducing maintenance costs, and enhancing equipment reliability and safety.
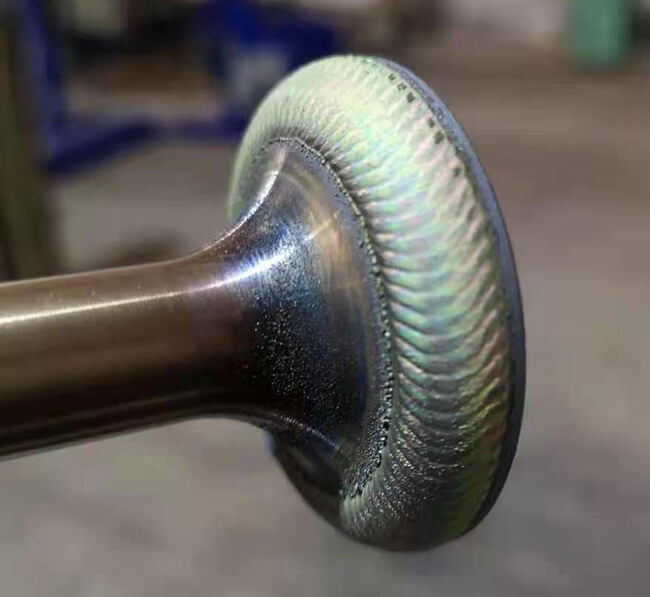
How to Implement Plasma Hardfacing (also known as Plasma Cladding) on Valves and Gates?
While there are various techniques for weld overlay cladding, the commonly utilized methods include Plasma Hardfacing (also termed Plasma Cladding) and Laser Cladding. In this article, we’ll primarily discuss the application of Plasma Hardfacing in the production and repair of Valves and Gates.
Plasma Hardfacing, an advanced welding method, employs high-energy plasma beams or arcs to generate localized high temperatures on the surfaces of Valves and Gates. This process melts the overlay material and the substrate surface together, forming a robust and hardened cladding layer. When compared to traditional welding techniques, Plasma Hardfacing exhibits more pronounced advantages.
Firstly, it offers greater precision: With Plasma Hardfacing, we can precisely control and position the cladding material, ensuring a more intricate and sturdy bond between the repair layer and the base material. Additionally, the deposited layer is densely packed, with low dilution rates, devoid of cracks and pores, smooth surfaces, and a typical thickness ranging from 0.5 to 5mm.
Secondly, its wear resistance is superior: The high melting temperature of Plasma Hardfacing, combined with its rapid cooling rate, produces a fine and compact overlay layer. This layer boasts excellent wear and corrosion resistance. Furthermore, it maintains these characteristics even under harsh working environments.
Lastly, Plasma Hardfacing is highly versatile: Suitable for various overlay and substrate materials, it can be applied to valves and gates made of different alloys. The range of materials isn’t restricted to metallic substances like cobalt, nickel, iron, and copper bases but also extends to non-metallics like ceramics. The versatility of Plasma Hardfacing is evident not just in its wide material applications, but also in its adaptability to various equipment. It’s suitable for manual operations and seamlessly integrates with automation tools, like robots, enabling automated, large-scale production. This ensures higher production efficiency, premium quality, and consistent results. Thus, the adaptable nature of the Plasma Hardfacing technique can fulfill diverse requirements.
In conclusion, Plasma Hardfacing technology is an invaluable method for repairing and protecting valves. It significantly extends the lifespan of our equipment, reduces replacement or maintenance costs, and is increasingly being recognized and employed across various sectors.
Application of Plasma Hardfacing Technology in the Valve Industry:
Plasma Hardfacing technology has widespread applications within the valve sector, including but not limited to: Valve rings, Ball valves, Valve clacks, Gauge valves, Valve seats, Power station valves, Brake valve plates, and Inner cladding.
A specific application example: The Triple-offset Valve Plasma Hardfacing System.
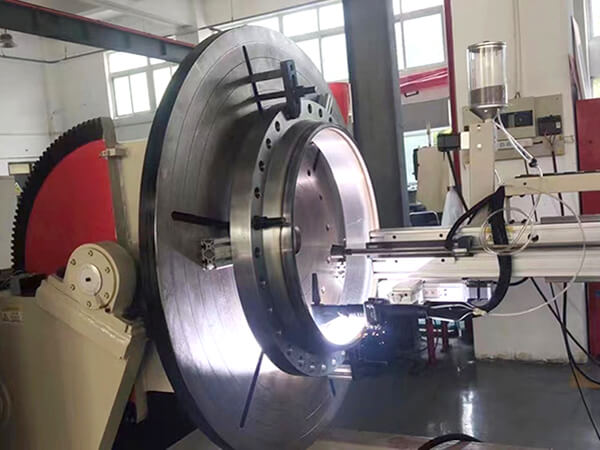
The most common welding equipment we use for valves combines the Welding Positioner with a cross-shaped welding bracket. While this structure has broad versatility and can accommodate the automated welding of various shaped components, it doesn’t quite meet the needs presented by the unique shape of triple-offset valves. Therefore, Deewi Automation has custom-designed a dedicated Plasma Hardfacing system for these valves (as illustrated in the following image). This not only enhances the welding efficiency but also yields superior weld quality.
Furthermore, Deewi Automation has also developed customized equipment for various other client requirements, such as:
- Robotic welding equipment with offline programming capabilities: Adaptable to various types and models of products, its offline programming significantly eases our tasks and offers a more convenient operation.
- Welding machines compatible with both wire and powder: Recognizing clients’ diverse requirements for welding materials, our machine is equipped with both wire feeding and powder feeding apparatuses. These can be switched interchangeably, catering to the diverse material requirements and greatly saving on equipment procurement costs for our clients.
- Multi-station welding production lines: This facilitates simultaneous operations from multiple angles, substantially boosting our work efficiency. It’s an ideal solution for large enterprises aiming for efficient, automated production. The system operates continuously, catering to our expansive production needs.
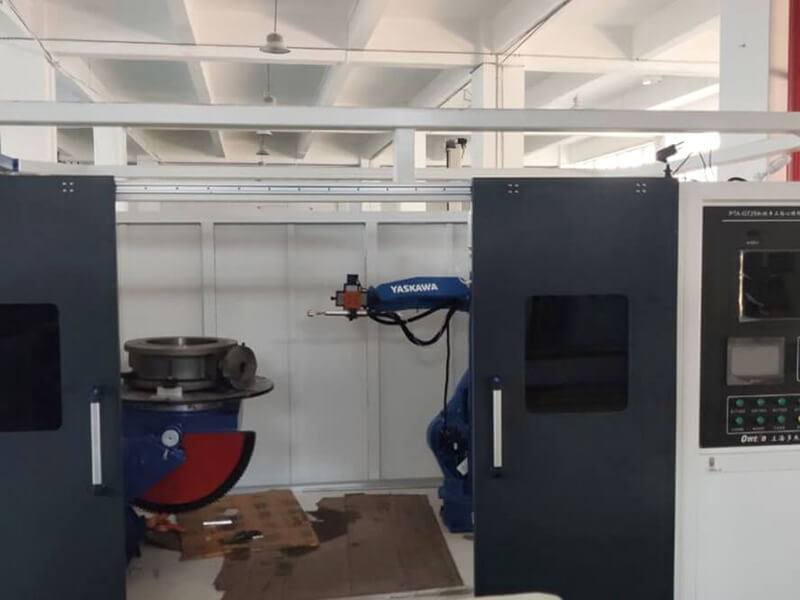
Robotic welding equipment with offline programming capabilities.
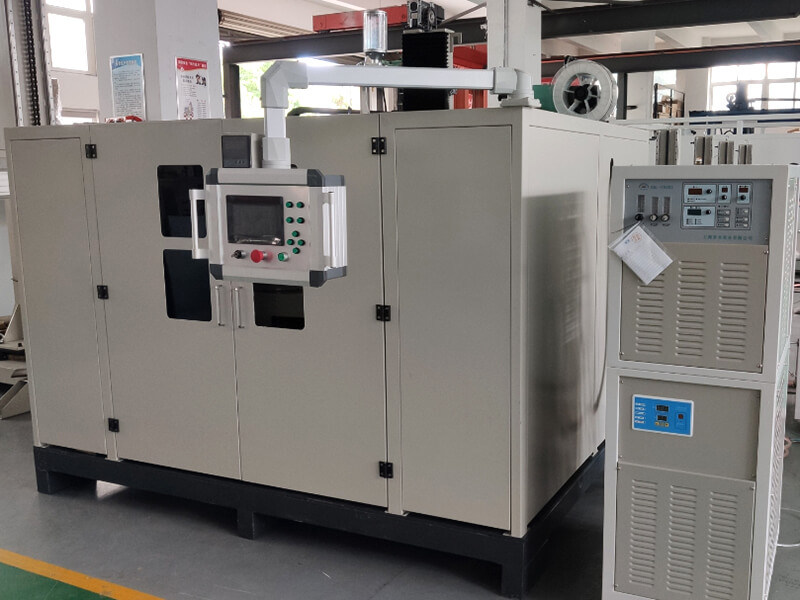
Welding machines compatible with both wire and powder.
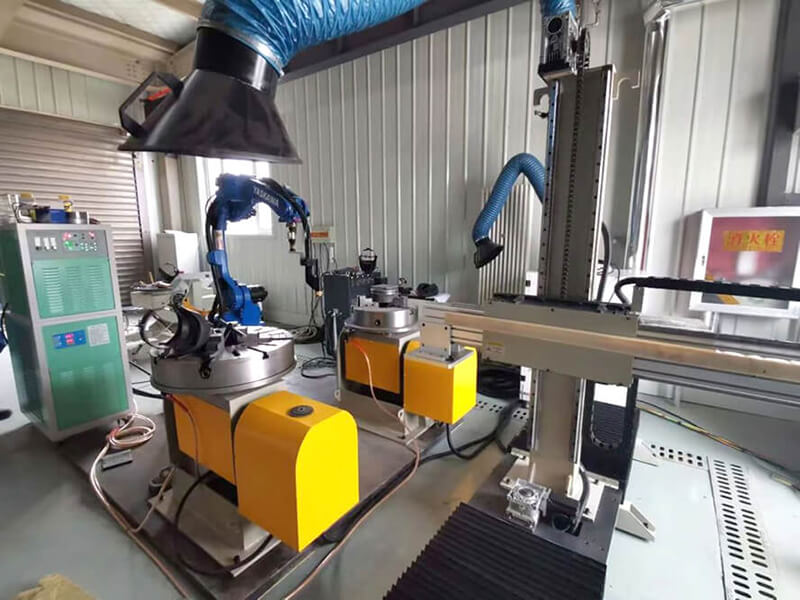
Multi-station welding production lines: This facilitates simultaneous.
Deewi Automation recognizes that within the valve industry, myriad issues continually arise: flawed designs, manufacturing oversights, careless maintenance, poor material selection, improper heat treatments, lax assembly, and more. Many of these issues pertain to damages on the valve sealing surface. A sealing surface that’s either too hard or too soft is incapable of withstanding wear. Moreover, even under standard operations, it’s impossible to avert the wear and erosion inflicted by the transported medium on the sealing surface. Given the high-temperature and high-pressure conditions, mechanical damages are inevitable. Hence, welding a protective layer onto the sealing surface is crucial. Want to know more. Deewi Automation are experts in this field, and we’re more than willing to assist you in tackling the various challenges you encounter.