Understanding the Application of Micro Plasma Welding Technology in Guidewire Tip Forming
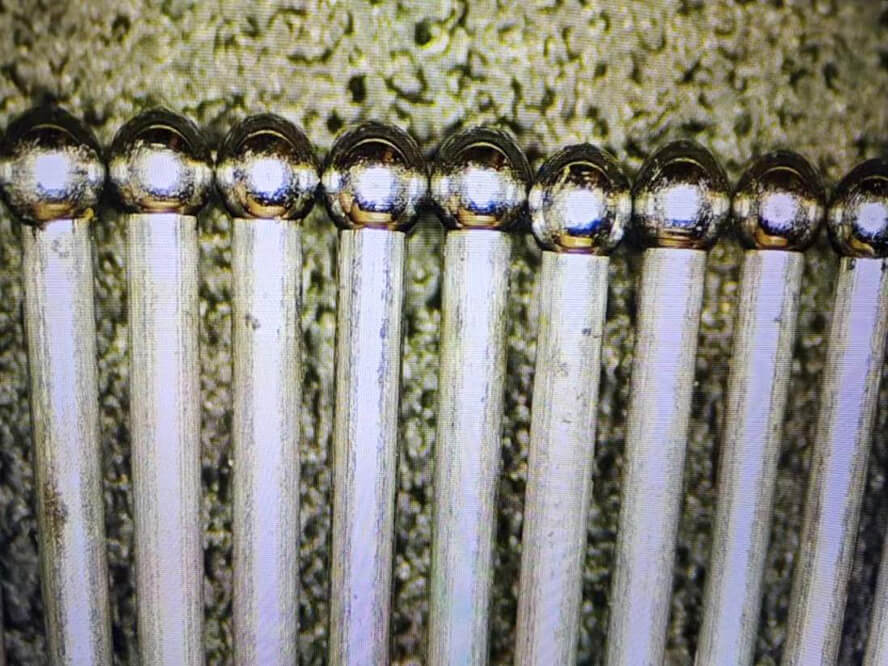
Why are guidewire tips designed to be spherical?
Guidewires are commonly used in the medical field, often featuring spherical or conical tips. This design is crucial for practical and clinical purposes, including:
- Reducing Tissue Damage: A spherical or conical tip, being smooth and rounded, minimizes the risk of damaging tissues when the guidewire contacts blood vessels or other tissues. This helps reduce patient discomfort and the likelihood of complications, especially in vascular insertion or catheterization procedures.
- Enhancing Navigation and Operability: Spherical tips enable easier control and guidance of the guidewire. In complex and winding vascular systems or other bodily channels, a spherical tip can smoothly navigate through curves and narrow passages, making it easier to find the correct path.
- Lowering the Risk of Misguidance: In practice, the tip of the guidewire is usually inserted first, followed by other medical devices or catheters. A spherical or conical tip can reduce the risk of misguidance, ensuring more effective guidance of subsequent devices.
- Enhancing Tactile Feedback: During precise operations, a spherical tip can provide better tactile feedback, allowing physicians to more accurately sense the guidewire’s position and movement within the vessel.
Overall, the spherical tip design of guidewires improves safety, flexibility, and operability in interventional surgeries, while reducing patient discomfort and tissue damage. This design is a well-thought-out aspect of medical device engineering, addressing specific clinical needs and functionality of catheters.
How does a micro plasma welding machine perform guidewire tip forming?
Given the small diameter of medical guidewires used in blood vessels, traditional manufacturing and shaping processes can be challenging. Micro plasma welding machines offer an efficient solution with their precise welding technique, making them particularly suitable for manufacturing tiny components or precision assemblies. When a high-energy-density plasma beam is applied to the tip of a guidewire, it instantly melts it into a liquid state. The internal stress then shapes it into a smooth, spherical tip. Micro plasma welding provides concentrated heat, easy control, excellent shaping outcomes, minimal thermal impact, and compatibility with various materials. It enables high work efficiency and easy automation.
In summary, using micro plasma welding machines for spherical tip forming offers numerous advantages, such as high precision, excellent shaping, strong controllability, automation, and high production efficiency, making it an ideal choice for manufacturing miniature medical devices and precision components. If you are interested in learning more about “micro plasma welding technology” or “guidewire tip forming,” feel free to contact us at Deewi Automation for professional advice and discussion on your queries.
Understanding Micro Plasma Welding and Ball-tip Weld Forming Technology: Common Questions and Answers:
Question 1: What is ‘Ball-tip Welding’ technology?
Answer 1: ‘Ball-tip Welding’ technology is a specialized welding technique using a micro plasma welding machine to create spherical tips on components. This method is commonly applied in manufacturing tiny parts, such as spherical tips on medical guidewires in medical devices.
Question 2 How does ‘Ball-tip Welding’ technology work?
Answer 2: ‘Ball-tip Welding’ employs a micro plasma welding machine to generate a high-frequency electric arc that melts the tip of the welding material. Under internal stress, the molten tip forms into a spherical shape. This welding process requires precise control and adjustment of welding parameters.
Question 3: What are the costs associated with ‘Ball-tip Welding’ technology?
Answer 3: The costs of ‘Ball-tip Welding’ technology vary depending on the specific applications, machine models, performance specifications, and the manufacturer chosen. Generally, the equipment and operational costs are not very high, especially when compared to micro laser welding technology, which tends to be more expensive.
Question 4: How is quality control managed in guidewire Ball-tip Weld forming? Is it possible to conduct visual inspections?
Answer 4: Quality control typically involves monitoring and adjusting welding parameters to ensure outcomes meet the set requirements and standards. Using electron microscopes or other visual inspection tools, the spherical welded tips are examined to verify their shape, size, and surface quality align with welding specifications.
Question 5: What are the main challenges faced in Ball-tip Welding technology?
Answer 5: The main challenges in Ball-tip Welding technology include ensuring consistency and repeatability in the welding process, maintaining uniform quality in batch welding, ensuring consistent dimensions and surface quality, and preventing material damage or deformation during welding.
Question 6: Are there any material limitations for Ball-tip Welding technology?
Answer 6: Although this technique is suitable for various metals like stainless steel and titanium alloys, different materials have varying melting points, thermal conductivity, and chemical stability, necessitating distinct welding parameters. The chemical or physical properties of materials can impact welding outcomes, so tailored welding plans are needed based on the material properties.
Question 7: Is training required to operate this technology?
Answer 7: Yes, operating a micro plasma welding machine typically requires specialized training to ensure safe and skilled handling of the equipment for high-quality welding.