Comparison of TIG, MIG, and MAG Welding Techniques
An in-depth comparison of TIG, MIG, and MAG welding processes to help you make the right equipment choice.
- Definitions of TIG, MIG, MAG, and Common Welding Techniques
- Comparison of MIG, MAG, and TIG Welding Techniques
- TIG Welding Features and Applications
- Comparing Materials for MIG and TIG Welding
Definitions of TIG, MIG, MAG, and Common Welding Techniques
SMAW (Shielded Metal Arc Welding)
Also known as Stick welding, SMAW involves generating an arc between a coated electrode and the base metal. The heat from the arc melts both the electrode and the base metal. The coating on the electrode melts to stabilize the arc, form slag, deoxidize, and refine the weld.
Welding power sources typically use an AC or DC arc welder with a descending characteristic. AC arc welders are commonly used, while DC arc welders are preferred when high arc stability is required.
Key Features: Simple operation, lightweight welding holder, easy mobility, and a wide range of applications.
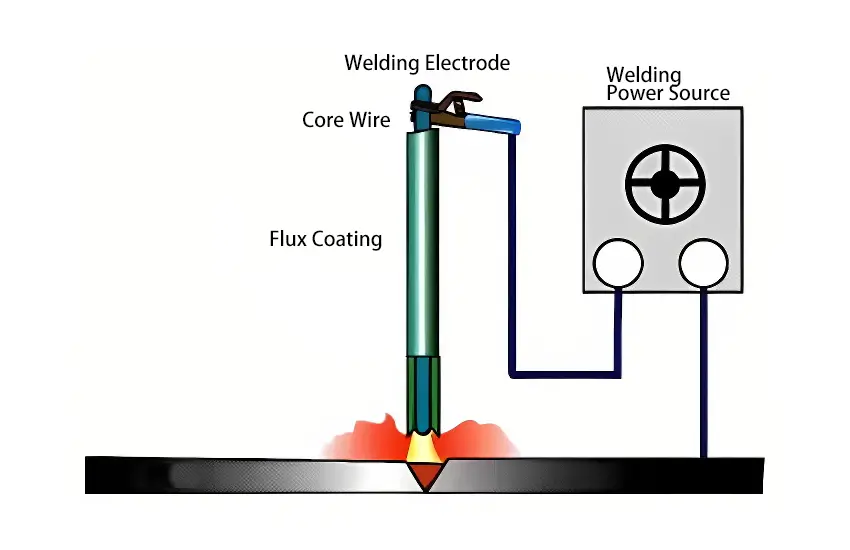
GMAW (Gas Metal Arc Welding)
Also known as MIG (Metal Inert Gas) welding, this method generates a high-energy arc between a wire electrode and the base metal, with shielding gas protecting the weld area. It is commonly used in automotive applications, including handheld welding guns and robotic welding.
Based on the shielding gas, GMAW is divided into:
- MAG Welding (Metal Active Gas Welding): Uses active gases like CO2 or O2 mixed with inert gases.
- MIG Welding (Metal Inert Gas Welding): Uses inert gases like argon, suitable for welding non-ferrous metals.
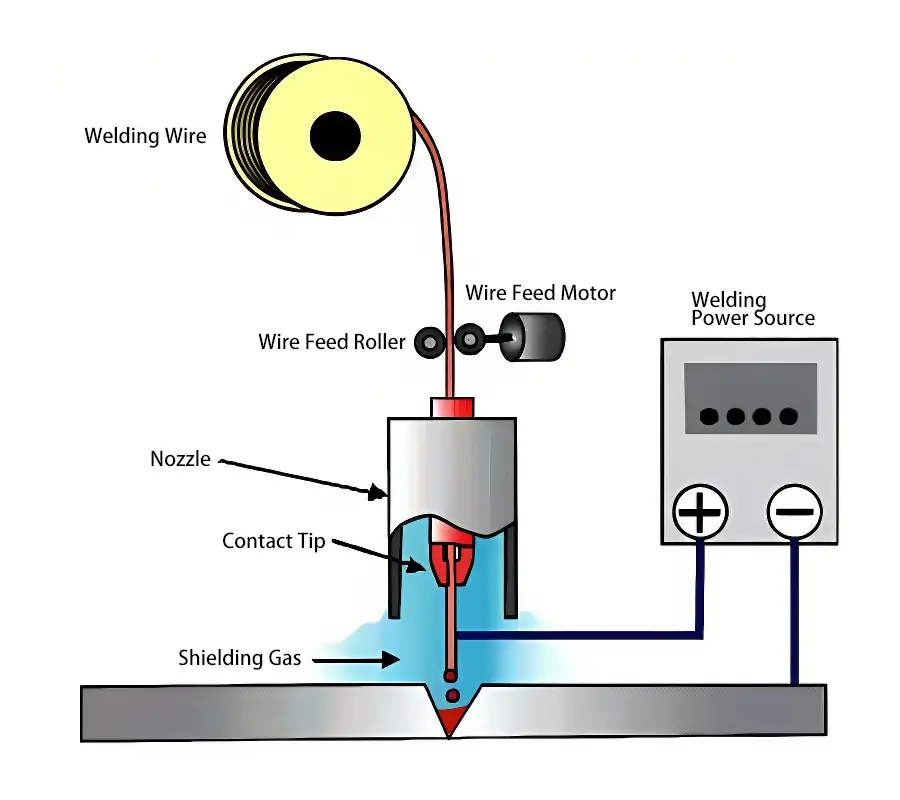
TIG Welding (Tungsten Inert Gas Welding)
TIG welding uses a tungsten or tungsten alloy electrode under an inert gas shield to generate an arc that melts the base metal and filler rod. It is also known as GTAW (Gas Tungsten Arc Welding).
DC TIG Welding
Uses a DC power source with the electrode as the negative pole and the base metal as the positive pole. It is widely used for welding stainless steel, titanium, copper, and copper alloys.
AC TIG Welding
Uses an AC power source with alternating positive and negative polarity of the electrode and base metal. The positive electrode removes surface oxides from the base metal, a process known as cleaning. This method is widely used for welding aluminum and magnesium.
Key Features: Suitable for welding almost all industrial metals and alloys, high welding quality and reliability, excellent weld appearance, no slag removal, minimal spatter, low smoke, and applicable to various material thicknesses.
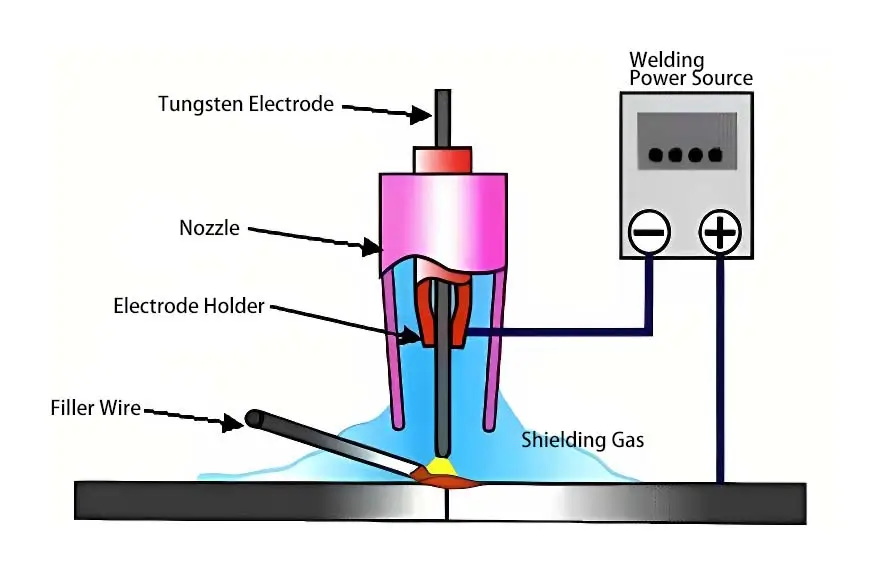
Comparison of MIG, MAG, and TIG Welding Techniques
- TIG Welding: Typically involves holding the welding torch in one hand and the filler rod in the other, suitable for small-scale operations and repair work.
- MIG and MAG Welding: The wire electrode is fed automatically from the welding gun, suitable for automated welding but also usable for manual welding.
- Difference Between MIG and MAG Welding: Mainly lies in the shielding gas. MIG uses inert gases like argon, suitable for welding non-ferrous metals. MAG uses active gases mixed with argon, suitable for welding high-strength and alloy steels.
- Comparison of TIG and MIG Welding: MIG welding uses a metal wire instead of a tungsten electrode. Both are inert gas shielded arc welding processes, often called argon arc welding. MIG uses argon mixed with 1% oxygen to stabilize the arc, unlike TIG.
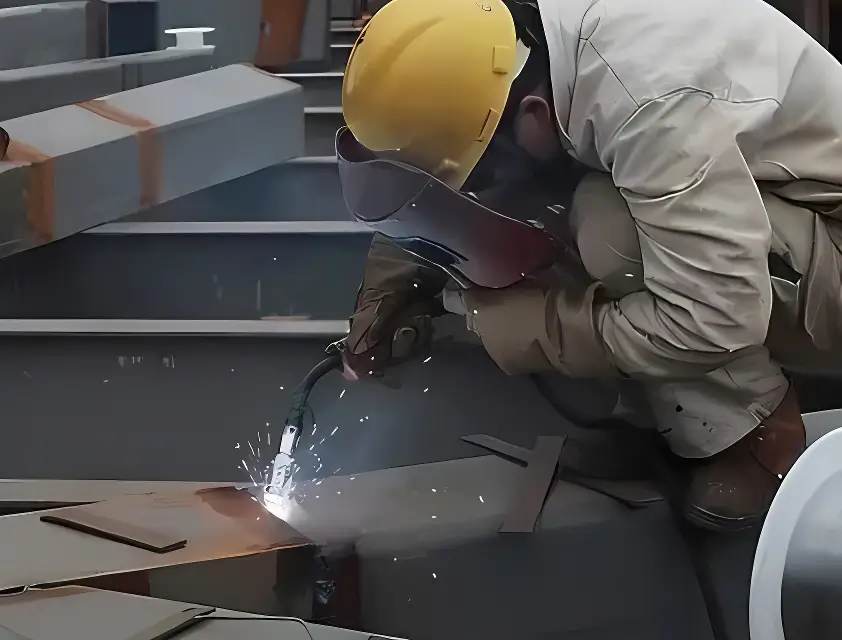
TIG Welding Features and Applications
TIG Welding Setup:
- Connection: Workpiece connected to the positive pole, tungsten electrode in the torch connected to the negative pole.
- Heat Source: DC arc with a voltage of 10-95V and a current up to 600A.
- Shielding Gas: Typically argon, sometimes mixed with 5% hydrogen for increased heat input. Gas flow rate is 3-8 liters per minute. Additional shielding from beneath the weld seam is recommended.
Applications:
TIG welding is widely used due to the protective argon shield, which prevents oxidation. It is ideal for:
- Oxidation-prone non-ferrous metals like aluminum, magnesium, and their alloys.
- Stainless steel, high-temperature alloys, titanium, and titanium alloys.
- Refractory metals like molybdenum, niobium, and zirconium.
TIG welding is preferred for high-quality welds on pressure vessels, ensuring good gas-tightness and reducing weld porosity.
Comparing Materials for MIG and TIG Welding
Both MIG and TIG welding can handle almost all metals, particularly aluminum and its alloys, copper and its alloys, and stainless steel. The welding process minimizes oxidation and evaporation losses, making the metallurgical process simpler.
By understanding the differences and applications of TIG, MIG, and MAG welding methods, you can select the best technique for your specific needs.