Innovative application of laser cladding technology in pump valve repair
In the current industrial production process, pump valves are key equipment for controlling fluid transmission, and their stability and durability are crucial to ensuring production continuity and safety. However, due to long-term exposure to high-speed fluids, particle erosion and corrosive environments, wear and damage to pump and valve equipment is inevitable. Traditional maintenance methods, such as welding repairs and replacing parts, are often costly and time-consuming. As a modern surface engineering technology, laser cladding technology provides an efficient, economical and environmentally friendly new solution for pump and valve maintenance.
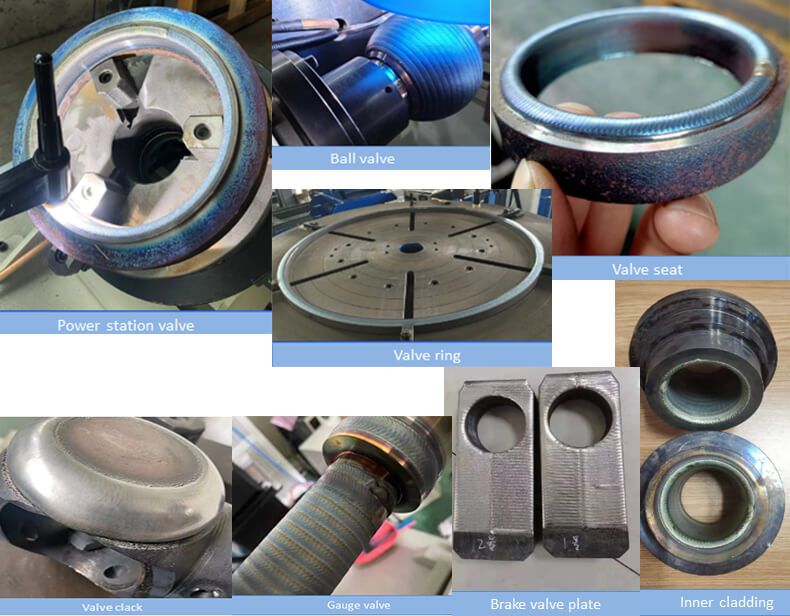
The principle of laser cladding technology is to use a high-power laser beam as a heat source to melt the additive material (usually powder or filament), and at the same time metallurgically bond it with a small area on the surface of the base material to form a layer of wear-resistant and corrosion-resistant protection. layer. The innovative application of this technology in pump and valve maintenance is mainly reflected in the following aspects:
- Precise positioning and rapid repair: Laser cladding technology can accurately control the cladding area and repair only the worn parts without affecting other parts of the pump valve. Compared with traditional repair processes, the delicate operation of laser cladding can complete the repair work in a few hours, greatly reducing downtime.
- Improve component performance: Repair is not just about restoring original performance. Laser cladding can improve the performance of repaired components by selecting powders that are better than raw materials, such as high-hardness alloys and corrosion-resistant materials. This not only extends the life of the components but also improves overall equipment efficiency and reliability.
- Reduce maintenance costs: Since laser cladding can be performed in situ, the complex process of dismantling and transporting equipment is avoided, thereby reducing maintenance costs. In addition, laser cladding has a high material utilization rate, reducing material waste and further reducing the material cost of repairs.
- Extend the maintenance cycle: The new layer formed by laser cladding has excellent bonding strength and density and can withstand longer operating challenges, which means that the maintenance cycle of the pump valve can be significantly extended, reducing the need for frequent maintenance. need.
- Environmentally friendly: Compared with traditional welding and other heat treatment processes, the laser cladding process produces less smoke and harmful gases, which meets the current environmental protection requirements of industrial production.
In specific pump and valve maintenance applications of laser cladding technology, it is necessary to select appropriate cladding materials and process parameters based on the working environment and wear types of different pump valves. For example, when dealing with seawater pump valves, copper-based or nickel-based alloys may be selected as cladding materials to improve their corrosion resistance; while for pump valves conveying abrasive media, tungsten carbide or ceramic materials may be selected to improve their corrosion resistance. Its wears resistance.
In the future, with the further development of laser technology, the accuracy and efficiency of laser cladding will continue to improve. Combined with automation technology and intelligent control systems, laser cladding will be able to achieve a higher degree of automation and better repair results, bringing revolutionary changes to the field of pump and valve maintenance.