Laser Surface Hardening Technology: A Modern Industrial Innovation
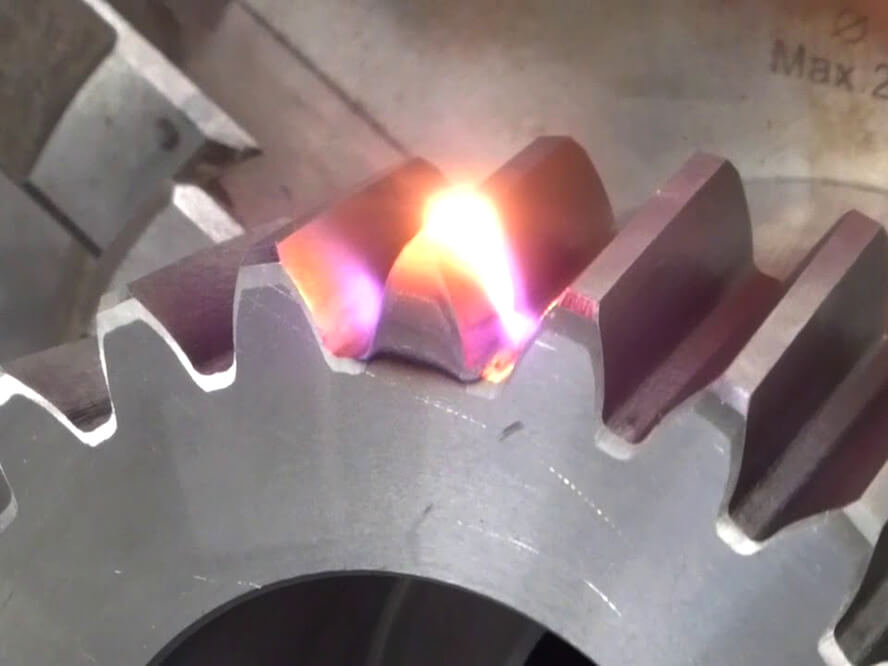
What is Laser Surface Hardening?
Laser surface hardening is an advanced material heat treatment process that enhances the surface hardness of materials, thereby improving their wear resistance. This technique involves rapidly heating the metal’s surface layer with a high-energy-density laser beam, raising the temperature to the phase transformation point without melting the surface. Notably, the underlying metal does not significantly heat up during this process. Once the laser moves to the next area, the surface layer rapidly cools, a phenomenon also known as “self-quenching.” This rapid heating and cooling process changes the microstructure of the metal surface, forming a hard martensitic structure, defining the laser surface hardening process.
Compared to traditional heat treatments, this method offers advantages like better control, high precision, efficiency, minimal heat-affected zones, no need for additional cooling media, flexibility, and eco-friendliness. It’s particularly suitable for complex-shaped components like gears, bearings, and molds, which often endure significant wear.
The Laser Surface Hardening Process
The laser surface hardening process typically involves several key steps:
- Pre-treatment Preparation: Before beginning the hardening process, it’s crucial to clean the target component, removing oil, rust, or other impurities. This step significantly impacts the effectiveness of the subsequent hardening.
- Setting and Adjusting Laser Parameters: Parameters like laser power, scanning speed, and focus distance must be precisely set based on the component’s shape, material characteristics, and desired hardening depth. The accuracy of these settings directly affects the hardening outcome and consistency.
- Laser Scanning: The laser hardening equipment scans the area to be hardened. The laser beam parameters are adjusted to rapidly heat the metal surface to the phase transformation temperature without melting it. Accurate temperature control during this step is crucial to the effectiveness of the hardening process.
- Self-Quenching Process: After laser heating, the surface layer rapidly cools, referred to as “self-quenching.” This fast heating and cooling process helps form a hard martensitic structure, enhancing the part’s surface hardness and wear resistance.
- Quality Inspection: After the laser hardening process, a quality inspection is conducted. This includes checking the hardness and microstructure to ensure it meets the hardening standards.
- Post-Processing: After hardening, the part may undergo further processing, like grinding, cleaning, or coating, to ensure its dimensions, surface quality, and appearance meet the set requirements.
By following these steps, products can significantly increase their wear resistance, extending their lifespan. Compared to traditional heat treatments, this method is more flexible, efficient, and environmentally friendly.
Advantages of Laser Surface Hardening:
Why Choose Laser Surface Hardening?
Laser surface hardening technology, known for its uniqueness, is increasingly replacing traditional heat treatment processes in modern industrial sectors. Compared to conventional hardening techniques, laser hardening offers higher efficiency, accuracy, convenience, and improved quality of the hardening process. Here are some key advantages of laser surface hardening:
- Excellent Controllability and Precision: Laser hardening is a localized process, allowing for high-precision control over the treated area. You can precisely set the laser’s power and scanning path, making it suitable for complex or irregularly shaped parts. Precise temperature control enables accurate hardness in different areas. Moreover, the entire process can be automated, ensuring precise and consistent results.
- Minimal Heat-Affected Zone, Reduced Material Deformation: As laser hardening is a localized heating method, it minimizes the heat-affected zone. This results in little overall structural or shape distortion of the part, crucial for components requiring high dimensional accuracy.
- Environmentally Friendly: The laser hardening process is clean, requiring no additional cooling mediums or fuels, leaving the product surface clean and eliminating the need for post-processing. This makes the process more environmentally friendly and conducive to better working conditions.
- Self-Quenching Effect: The rapid heating and subsequent rapid cooling, known as “self-quenching,” aids in the material undergoing a phase transformation to form a harder martensitic structure, thus achieving the hardening and enhancing wear resistance.
- Flexible Operation, Good Adaptability: Laser hardening technology can treat complex and irregular parts, with fewer requirements for the operating site. Unlike traditional heat treatment processes that require complex procedures and equipment, laser hardening offers more flexibility and adaptability.
In summary, laser surface hardening, with its excellent precision, minimal material distortion, and clean, eco-friendly process, is becoming the best choice for enhancing the surface performance of many metal parts. It effectively increases surface hardness, wear resistance, and service life, significantly saving production costs and becoming an indispensable key technology in specialized industrial fields.
Industrial Applications of Laser Surface Hardening
Laser surface hardening, as a precise and efficient material processing technology, has widespread applications across various industries. It not only enhances product performance and durability but also plays a vital role in improving production efficiency and reducing costs. Below, we briefly list its applications in different industrial sectors:
- Automotive Manufacturing: In this field, laser surface hardening is used to treat gears, bearings, camshafts, and other critical components. These parts often endure high loads and wear, and laser hardening improves their wear resistance and fatigue strength, extending their lifespan.
- Aerospace: The aerospace sector demands high-performance parts. Laser surface hardening can enhance the corrosion and wear resistance of key components in aerospace engines and landing gear, adapting them to extreme operating environments.
- Large and Heavy Machinery and Equipment: For heavy machinery, components like rolling mill shafts, hydraulic cylinders, and other heavy-load-bearing parts can have their surface hardness and performance enhanced through laser hardening, improving the overall equipment performance and durability.
- Molds and Tools: In the manufacturing of molds and tools, laser surface hardening can increase the surface hardness and wear resistance of cutting tools and molds without causing deformation. This not only extends their service life but also ensures high precision in their manufacturing processes.
- Medical Devices: In medical device manufacturing, laser hardening can be applied to surgical tools and implantable devices, ensuring their long-term safe and effective use.
With its unique process characteristics, laser surface hardening has become a key technology in certain sectors of industrial manufacturing. In these areas, laser hardening technology continues to revolutionize and reshape production methods.
Application Cases of Laser Surface Hardening:
Laser Surface Hardening of Cast Iron and Stainless Steel:
Laser surface hardening technology is widely used in cast iron and stainless steel materials, significantly enhancing their performance and durability. The carbon content in steel materials directly affects the surface hardness after treatment, with higher carbon content typically leading to higher hardness. However, materials with carbon content below 0.2% are not suitable for laser quenching.
- Laser Hardening of Cast Iron: Commonly used in mechanical, automotive, and construction castings, cast iron typically has a carbon content of 2%-4%. Therefore, its hardness is significantly enhanced after laser hardening, effectively improving the surface hardness and wear resistance of cast iron parts. This is particularly important for improving the performance and lifespan of heavily loaded cast iron components like gears and crankshafts.
- Laser Hardening of Stainless Steel: Known for its excellent corrosion resistance and aesthetics, stainless steel is widely used in food processing, medical equipment, and construction industries. The carbon content in stainless steel usually ranges between 0.1%-0.4%. Compared to traditional quenching processes, laser hardening can increase the surface hardness of stainless steel by 5%-20%, achieving a more refined and uniform hardened layer without compromising its corrosion resistance. This is particularly important for applications requiring high wear resistance and cleanliness, such as surgical tools and food processing equipment.
Laser hardening’s advantage lies in its ability to precisely control the heating area and depth, enabling precise control over the hardening effect and area while significantly reducing treatment costs.
Future Directions of Laser Surface Hardening Technology:
With continual advancements in modern technology and growing industrial production needs, laser surface hardening technology is set to expand across more fields and scenarios. The future development of this technology-driven field may exhibit the following characteristics:
- Innovation and Optimization of Technology: Future developments will likely bring continuous discovery and use of new technologies and processes in laser hardening. Focus will be on improving energy use efficiency and processing efficiency, while reducing environmental impact. Advances in lasers and intelligent control systems will aim for finer control and better hardening results.
- Expansion of Application Fields: With the ongoing development of new technologies, processes, and materials, laser surface hardening technology will find applications in more industrial settings, especially in sectors demanding high performance, precision, and durability.
- Integration with Other Technologies: Future enhancements will likely see laser hardening technology combined with various advanced technologies like 3D printing, intelligent robotics, and artificial intelligence. This integration will achieve higher automation and intelligence, continuously improving production efficiency and flexibility.
- Customized and Personalized Solutions: As the market demands for customized and personalized products grow, the processing equipment and techniques will evolve to meet various bespoke requirements.
Laser surface hardening technology is becoming a key driver in the future development of industries. It has improved industrial manufacturing processes in many fields and provided new solutions for precision manufacturing. We believe that as the process continues to evolve and costs decrease, it will find more extensive use and development in various applications. If you are interested in this technology, you are welcome to contact Deewi Automation to discuss and explore further.
In summary, using micro plasma welding machines for spherical tip forming offers numerous advantages, such as high precision, excellent shaping, strong controllability, automation, and high production efficiency, making it an ideal choice for manufacturing miniature medical devices and precision components. If you are interested in learning more about “micro plasma welding technology” or “guidewire tip forming,” feel free to contact us at Deewi Automation for professional advice and discussion on your queries, Learn more about Laser Surface Hardening.