Micro Plasma Arc Welding of Thin Stainless Steel Sheets: Weld Pool Size and Weld Quality Analysis
Abstract: This paper observes the changes of weld pool profile during pulsed Mcro plasma arc welding of 304 stainless steel thin sheets, and studies the influence factors of weld pool size and weld formation quality.
Results show that:
- When the average current is 1.8 A, the maximum width and area of the weld pool decrease gradually with the increase of the ratio of base current to peak current, duty cycle and pulse frequency;
- Three types of weld seams were obtained under different process parameters: discontinuous weld seam, continuous unequal width weld seam and continuous equal width weld seam;The best weld formation quality was obtained with a duty cycle of 50%, a ratio of base current to peak current of 0.50, and pulse frequencies of 25, 100, and 500 Hz, which is a continuous equal width weld seam;
- Under the experimental conditions, the measured weld pool width is all less than 2.5 mm, and the weld pool area is all less than 3.5 mm2.
1. Micro plasma arc welding principle and characteristics
1.1. Formation process and principle overview of microplasma arc welding:
Micro plasma arc is a type of plasma arc. Microplasma arc welding is generally referred to as plasma arc welding with a welding current below 30A.
For more information about conventional plasma welding, please refer to this page: Plasma welding.
Due to the small current condition, there are a series of special features in the morphology, stability of the plasma arc, its requirements for power supply and equipment, as well as the welding process and operation methods.
In order to improve the stability of the micro arc and further compress the arc, we reduce the size of the arc chamber and the gas flow. In this way, the micro plasma arc beam emitted by the reduced plasma welding torch nozzle can be as small as a sewing needle.
To maintain the stability of the arc at low current, a small orifice compressed nozzle (0.6~1.2mm) and a combined arc are generally used. In other words, there will be two arcs during welding, one is a non-transferred arc burning between the electrode and the nozzle, and the other is a transferred arc burning between the electrode and the workpiece. The former plays the role of arc initiation and arc maintenance, making the transferred arc very stable even when the current is as low as 0.5A. The latter is used to melt the workpiece.
For the common structure of micro plasma welding machines, please refer to the product page of our website: Micro plasma welding machine.
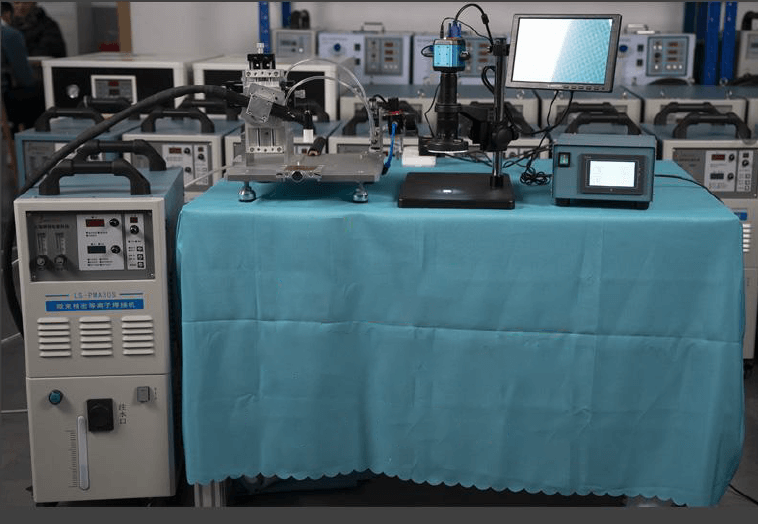
1.2. Key Components of Micro Plasma Arc Welding Machine for Generating Plasma Arc
Micro Plasma Arc Generator:
The micro plasma arc generator, also known as plasma welding torch or torch, is used to generate micro plasma arc. It is one of the key components for generating stable plasma arc. Requirements for a good micro plasma welding torch:- No gas leakage, no water leakage, no electricity leakage
- Electrodes are aligned
- Nozzles and electrodes are easy to adjust and replace
DC Welding Power Source
As the core component of micro plasma arc welding machine, the power supply of micro plasma arc welding machine requires higher adjustment precision than ordinary plasma arc welding power supply, which is convenient for fine adjustment of welding current. And it requires higher no-load voltage, usually 120~160V. Different from consumable parts such as welding torches, the quality of welding power supply largely determines the quality of the whole machine. Types of DC power source for micro plasma arc:According to the continuity of power supply, the DC power source for micro plasma arc can be divided into two types: continuous DC power source and pulse DC power source. As the name suggests, continuous DC power supply supplies continuous DC current, while pulse DC power supply supplies non-continuous and regularly fluctuating DC current. In addition to adjusting the current size, the pulse DC power supply can also control the on-time and interval time. Therefore, in practical use, the pulse DC power source is superior to the ordinary DC power source.
Inert Gas Source
In the arc chamber of plasma welding torch, the arc is formed under the action of mechanical compression effect, thermal contraction effect and magnetic compression effect. Two of the three compression effects are the action of inert gas. The inert gas used in micro plasma arc welding is generally argon. When using, the pressure and flow rate are precisely adjusted by the pressure reducing valve and flow meter.
1.3. Micro Plasma Arc Welding Process Parameter Setting
The main process parameters of micro plasma arc welding include: welding current, welding speed, working gas flow rate, shielding gas flow rate, arc length, nozzle diameter, nozzle bore ratio and tungsten electrode retraction. These parameters together determine the welding quality and weld shape.
The welding process parameters of common stainless steel thin plates can be referred to the following table:
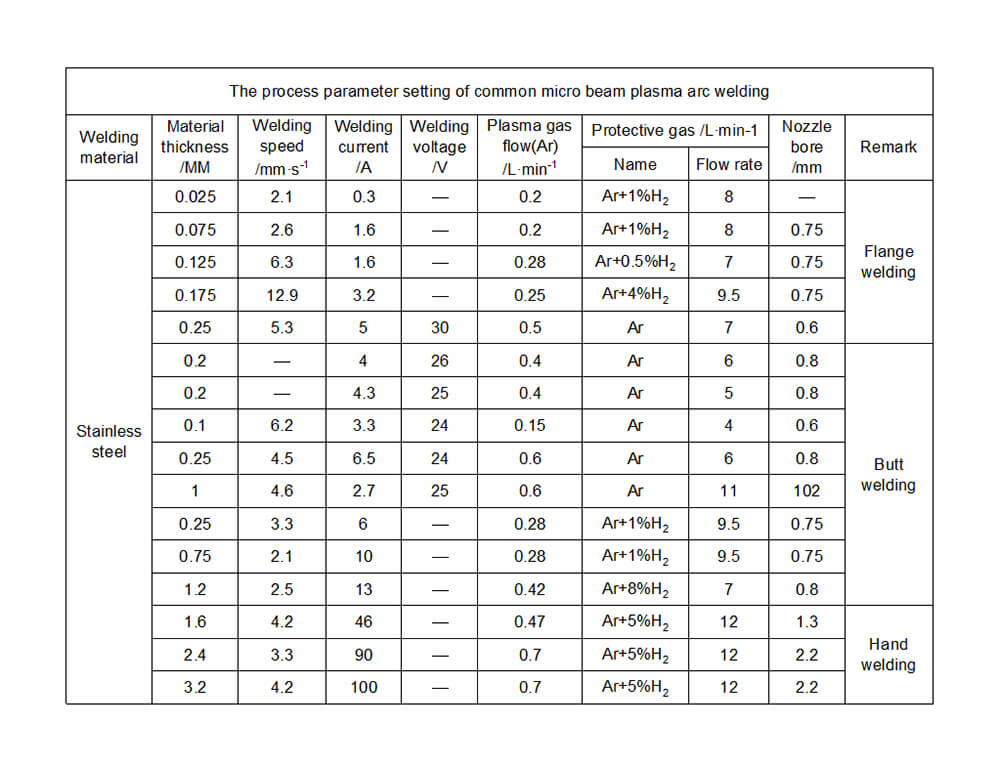
1.4. Advantages of Micro Plasma Arc Welding Compared with Conventional TIG Welding
- It can weld thinner metals, with a minimum weldable thickness of 0.01mm.
- The arc will not break even when the arc length fluctuates greatly, and the columnar characteristics can be maintained. The welding speed is fast, the weld seam is narrow, the heat affected zone is small, and the welding deformation is small.
2. Application and Quality Analysis of Microplasma Arc Welding in Ultra-thin Plates
2.1. Background
Ultra-thin plates are widely used in aerospace, rail transit, medical devices, precision electronics and other fields in industrial production. They are difficult to weld and require high precision. Microplasma arc welding technology is widely used.
Due to its very thin thickness, ultra-thin plates have the characteristics of single-sided welding and simultaneous double-sided forming. Moreover, it is particularly sensitive to welding heat input, and defects such as burn-through and deformation are prone to occur, which affects the welding quality. Therefore, we need to study the factors affecting the appearance and dimensions of the weld and weld pool.
We use a visual sensing detection system to collect image information of the weld pool during welding, and use MATLAB image processing software to analyze the geometric dimensions of the weld pool. The research on the changes in the morphology characteristics of the weld pool of 0.1 mm thick austenitic stainless steel ultra-thin plate using pulse DC power source under different process parameters provides a theoretical basis for improving the quality of ultra-thin plate weld in the future.
2.2. Experimental Preparation and Method
Specimen preparation: The experimental material is 0.1 mm thick 304 austenitic stainless steel sheet, with the Chinese material grade of 0Cr18Ni9.
Welding method: Before welding, wipe off the oil with alcohol and use the butt joint method for welding. Use the following detection equipment to observe the changes in the weld pool and collect data.
Welding process parameters:
- Welding speed: 4.1 mm/s.
- Torch height: 2 mm.
- Average current: 1.8 A.
- Shielding gas and plasma gas are both Ar, with flow rates of 3.5 L/min and 0.5 L/min respectively.
Other process parameters are shown in the following table:
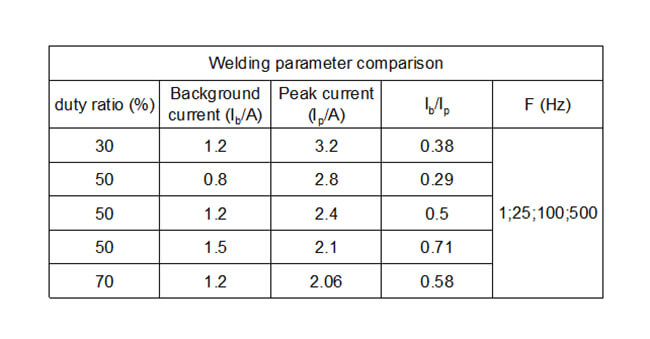
2.3. Experimental Results and Discussion
Weld pool size:
During the welding process with different process parameters, one weld pool image is captured every 50ms, and a total of 5 images are captured. The width and area of the weld pool are calculated by software, and the average value is taken.
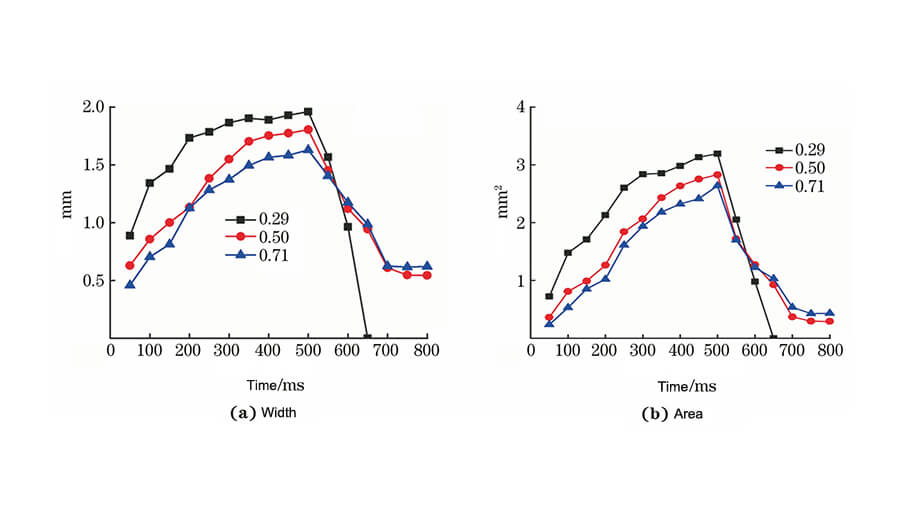
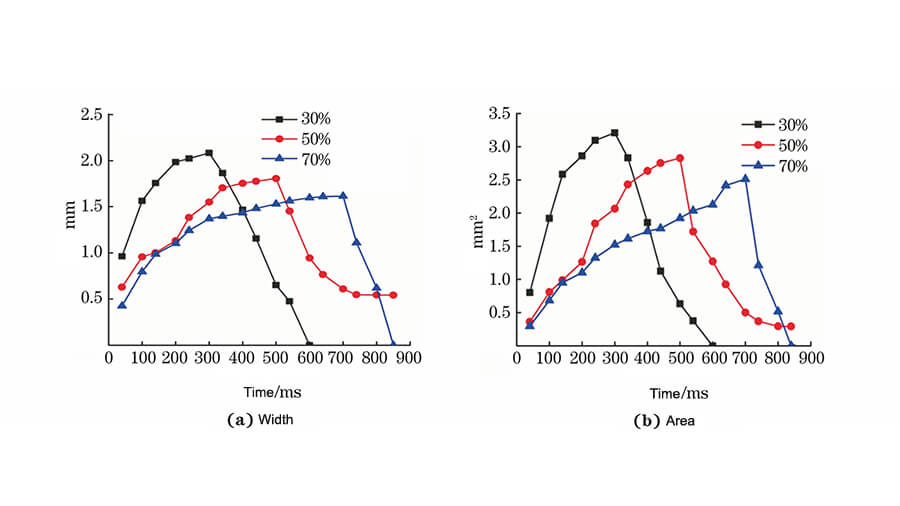
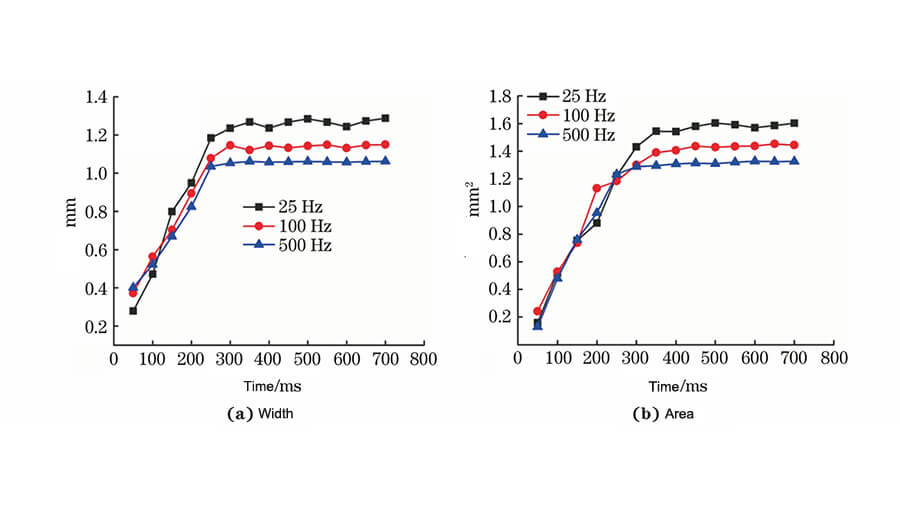
By adjusting and observing the influence of process parameters on weld pool size, I obtained the following data:
When the peak current is applied, the area and width of the weld pool gradually increase.
When the base current is applied, the area and width of the weld pool gradually decrease.
During welding, when the average current is 1.8A, the maximum width and maximum area of the welding weld pool decrease with the increase of base pulse ratio, duty cycle and pulse frequency.
Weld bead formation quality:
The weld pool size is closely related to the weld bead formation quality. Under the experimental process parameters, there are three different types of weld beads: intermittent weld bead, continuous unequal width weld bead and continuous equal width weld bead.
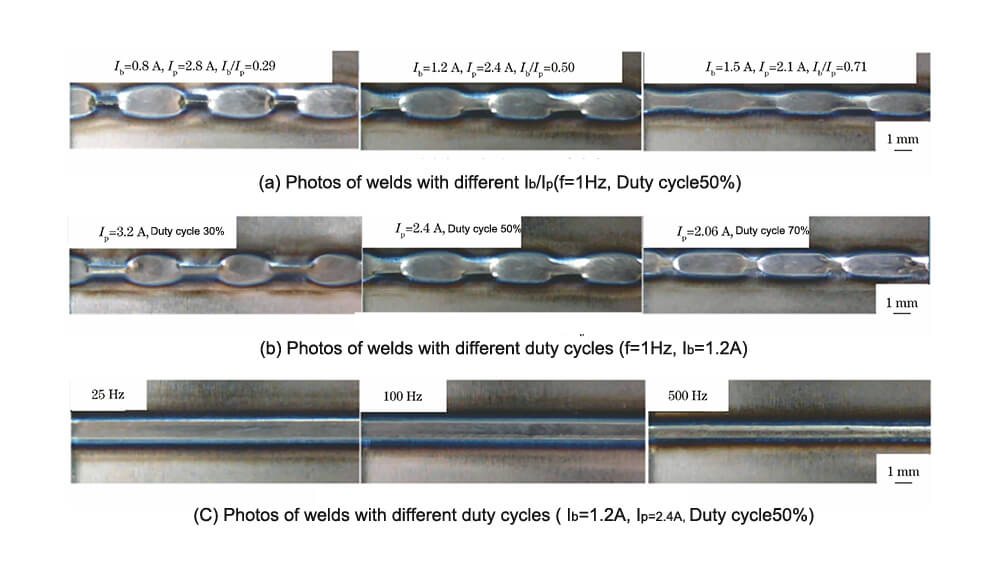
(b) weld at different duty cycle (f=11Hz Ib=1.2 A) and (c) weld at different pulse frequency (Ib=1.2 A Ip=2.4 A, duty cycle of 50%)
The best weld bead formation quality is obtained when the duty cycle is 50%, the base current is 1.2 A, the peak current is 2.4 A, the base pulse ratio is 0.50, and the pulse frequency is 25, 100, 500 Hz. The weld bead is a continuous equal width weld bead.
The results and analysis of the above experiments provide theoretical basis and data support for improving the quality of micro plasma arc welding of stainless steel thin plates in actual production.
However, in actual production, we can make some optimizations and adjustments based on the theory due to the influence of various factors such as the technical level of the operators and the conditions on site.
For the actual operation and use of the micro plasma welding machine, you can also refer to our Youtube video: