Micro Plasma Welding
Micro-plasma welding technology is known for its excellent welding precision and control, making it ideal for applications that place extremely high demands on joint quality. From medical devices to precision engineering, our product range is designed to meet all your precision welding needs.
Micro Plasma Arc Welding
Deewi Automation stands as a leading manufacturer, supplier, and exporter of top-notch Micro Plasma Welding (MPW) Machines. Utilizing the Precision Micro Plasma Arc Welding Machine with a welding current ranging from 0.1 to 40A, we offer unparalleled welding solutions. With our technology, you can achieve precise welding even on thin sheets, guidewires, and pipes as small as 0.1mm in size.
Our product range:Portable Micro Plasma Welding Machine: Designed for small studios and mobile operations, combining portability and high performance.
Benchtop microplasma welding systems: ideal for laboratories and manufacturing lines, offering more advanced control capabilities and automation options.
Customized microplasma welding solutions: customized for specific applications and production needs, including automated workstations and integrated systems.
Why Choose Our Micro Plasma Welding Solutions?
Choosing our micro-plasma welding products means choosing unparalleled precision and reliability. Our equipment is carefully designed and rigorously tested to ensure consistent, high-quality welding results in a variety of challenging conditions. No matter the size of your project, our dedicated team will provide you with personalized consultation to ensure you find the solution that best suits your needs.
What Is Micro Plasma Welding?
Micro Plasma Arc Welding (MPAW), a subset of Plasma Welding, Micro Plasma Welding is of the important arc welding process, shares similarities with TIG welding in terms of its arc formation. However, what sets it apart is its ability to adapt to various welding scenarios by adjusting nozzle apertures and plasma gas flow rates, resulting in three distinct energy modes: Micro plasma (0.1 to 15A), Medium current (15 to 100A), and Keyhole plasma (over 100A). Each mode finds its unique application.
Microplasma welding, in particular, is remarkable due to its stable, columnar arc. It exhibits exceptional precision, allowing for welding tasks on delicate materials such as sheets as thin as 0.1mm, intricate metal wires, and mesh structures. This technique finds widespread use in welding applications for medical guidewires, ball tip guidewires, Wire & Rod End Rounding, Wire Binding, Light Bulb Filaments, Wire Mesh Welding, and more.
If you have any questions about micro plasma welding technology or products, or need professional advice, don’t hesitate to contact our customer service team today. We are committed to providing the best support and solutions for your precision welding needs.
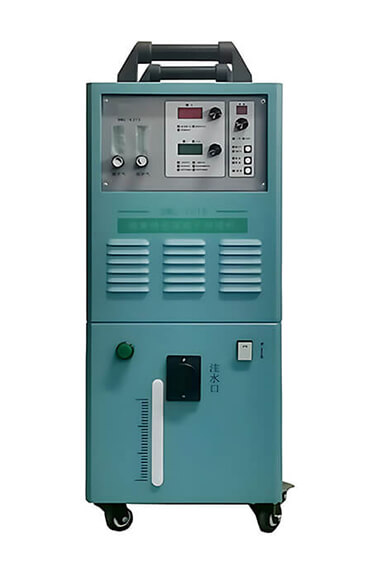
The composition of the Micro Plasma Arc Welding Machine.
The common components of a Micro Plasma Arc Welding Machine typically include:
Precision Micro Plasma Welding Machine Host Parameters
Benefits of Micro Plasma Welding:
Micro Plasma Welding can be considered an upgraded version of Tungsten Inert Gas (TIG) welding process. Its most significant feature is the ability to perform welding in very small dimensions with high precision. Beyond its capability to weld extremely small parts, Micro Plasma Welding offers several advantages:
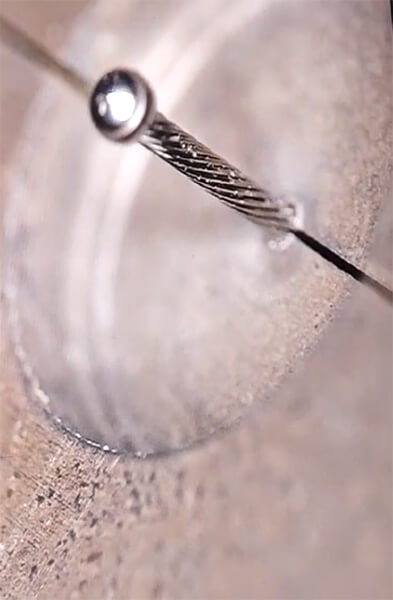
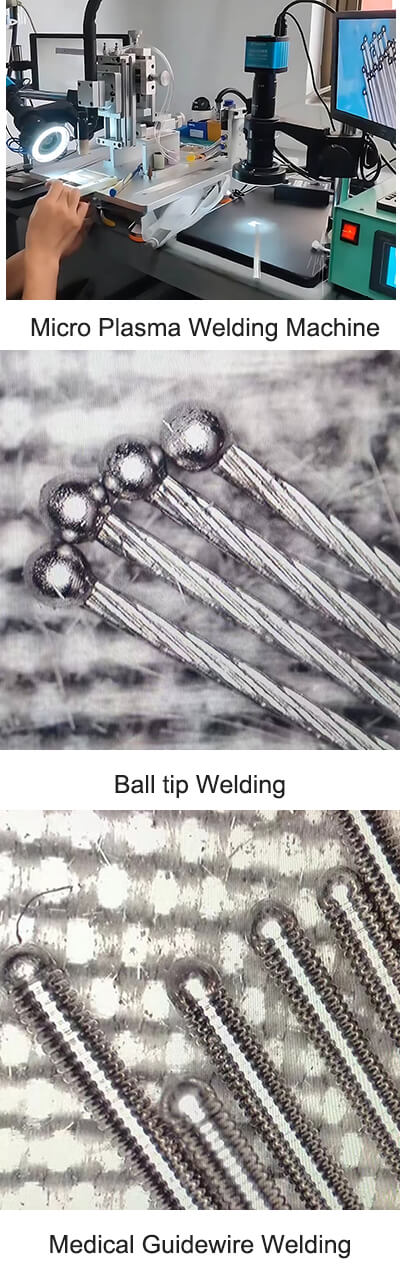
Quick Q&A – About Micro Plasma Welding.
Regarding ‘Micro Plasma Welding’, here are some common questions and their answers:
Micro Plasma Welding Process&Applications
The best partnerships often begin with your courageous attempts.
Deewi Automation Technology Co.,Ltd.
We are glad to offer technical solutions to people who are interested in our products. You just need to fill a form.
Get in touch with us today!