How much do you know about the “micro plasma welding machine”?
The Micro Plasma Welding Machine is a specialized welding equipment that employs precision plasma welding technology for precision welding and micro-component fabrication. Here are some basic insights about the Micro Plasma Welding Machine:
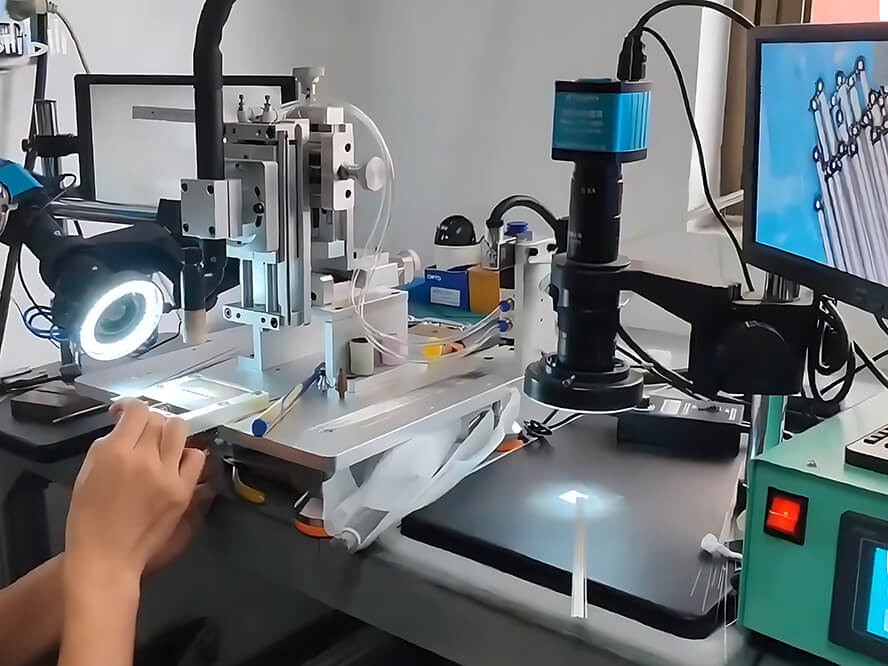
Micro Plasma Welding Process (Working Principle):
Micro Plasma Welding is a precision welding technique based on plasma welding principles, which utilizes an electric arc to heat gas, typically argon, creating a high-temperature plasma spark. This intense plasma spark is used to melt the welding material and the surface of the workpiece, achieving a weld. Micro plasma welding is often used for welding smaller scales or thin metal materials, especially in applications where high quality and precision in welding are required. Its working principle involves several key steps:
- Generating Plasma: Micro plasma welding generates high temperatures through an electric arc between a tungsten electrode and the workpiece, ionizing the gas (usually argon or a mix of argon and hydrogen) into plasma. Plasma, a high-energy state flow of free electrons and charged gas atoms (ions), has a high energy density capable of melting the welding surface in a very short time.
- Focusing the Plasma: Micro plasma welding machines use a special nozzle to focus the plasma beam into a micro, needle-like plasma stream, allowing for very fine and precise welding control. This focused plasma stream can produce very small welding spots, making it particularly suitable for welding tiny and precision components.
- Melting Material and Forming Welds: The high temperature of the plasma beam rapidly melts metal materials. When it acts on the tip of a wire or other components, the melted tip forms a spherical welding structure under internal stress. As the plasma beam moves, the molten metal forms a weld seam between the electrode and the workpiece. The small area and high energy density of the micro plasma beam allow for high-speed welding and minimize the heat-affected zone, which is beneficial for precision welding of temperature-sensitive or thin materials.
- Cooling and Solidification: Once the heat source moves away, the melted metal quickly solidifies during cooling, forming a robust metallurgical bond.
In summary, micro plasma welding machines melt welding material using high-frequency electric arc discharge to generate a plasma spark. The use of protective gas in welding prevents oxidation in the welding area, enhancing welding quality. Micro plasma welding machines are particularly suitable for applications requiring high precision and micro-fine welding. Operators can achieve various welding needs by adjusting and controlling welding parameters.
What Can Micro Plasma Welding Machines Be Used For? (Application Areas):
Micro plasma welding is typically used in the manufacturing of micro-components, such as electronic components, medical devices, Micro-Electro-Mechanical Systems (MEMS), optical components, and other areas requiring high-precision and micro-fine welding. With minimal heat-affected zones, micro plasma welding reduces material deformation and thermal damage while ensuring high precision. Common application areas for micro plasma welding machines include:
- Medical Devices: Micro plasma welding is extensively used in medical device manufacturing. Various precise medical equipment, implantable medical devices, and micro-surgical tools often require tiny, precision parts, which are frequently joined using micro plasma welding technology. For instance, the tip forming of medical guidewires often requires micro plasma welding to effectively create a spherical structure at the tip.
- Electronics Manufacturing: Micro plasma welding machines are also common in the electronics industry and Micro-Electro-Mechanical Systems (MEMS) for manufacturing micro-mechanical structures and electronic components, as well as for micro-fine electronic assembly. For example, when welding electronic components, micro-sensors, and micro-connectors, the high precision and controllable welding of micro plasma welding machines can provide the required quality and accuracy.
- Optical Components: In optics and laser technology, highly precise optical components are often needed. Micro plasma welding can be used to manufacture fiber optic connectors, laser diode (LD) packages, and other optical parts, where precision welding ensures the stability and accuracy of the component’s optical performance.
- Aerospace: In the aerospace sector, some micro-components also require high precision and micro-fine welding. For instance, in manufacturing satellite components, space probes, and spacecraft, micro plasma welding joins tiny parts to ensure their reliability in extreme conditions.
Overall, micro plasma welding machines play a key role in various applications involving high precision, micro-fine welding, and precision manufacturing. The high precision of micro plasma welding, high-quality connections, and minimal heat-affected zone make it significant for manufacturing small parts or precision components.
Characteristics and Advantages of the Micro Plasma Welding Machine:
Compared to traditional welding methods, the Micro Plasma Welding Machine possesses several features that give it significant advantages in certain applications. Here are some key characteristics and benefits of the Micro Plasma Welding Machine:
- Features of Micro Plasma Welding Equipment: Typically, these machines have a high level of automation, allowing for precision welding through computer programming and control. They are usually equipped with a gas control system to manage the plasma spark and protect the welding area from external environmental factors.
- Stable Arc: The electric arc generated by micro plasma welding is very stable, even at very low currents.
- High-Quality Welds: These machines deliver high-quality welding, producing strong, visually appealing welds with high strength and minimal defects like porosity.
- Precision Welding: Micro plasma welding machines enable highly precise welding and exceptional welding control, crucial for manufacturing small parts and precision components.
- Minimal Heat-Affected Zone: Compared to other welding methods, micro plasma welding generates a smaller heat-affected zone, reducing thermal deformation and material distortion. This is vital for maintaining dimensional accuracy and material properties of precision parts.
- Welding of Fine and Thin Materials: Micro plasma welding technology is particularly suited for fine welding, handling small welding components or narrow welding areas without causing deformation. It’s also ideal for welding thin sheet materials, reducing the risk of burn-through.
- Fast Welding Speed: Micro plasma welding has a relatively fast welding speed, enhancing efficiency and helping reduce manufacturing costs.
- Automation Capability and Repetitiveness: The micro plasma welding process is easily automated, controllable through computer programming, reducing the risk of operator error. This ensures high repeatability and consistency in mass production.
- Adaptability and Control: Micro plasma welding adapts to various working environments and materials, including stainless steel, aluminum alloys, titanium alloys, and other metal alloys, even some that are challenging to weld using conventional methods. Operators can precisely control the welding process by adjusting parameters like current, voltage, welding speed, and wire feed rate, meeting different application needs.
In summary, the micro plasma welding machine offers numerous advantages such as high precision, fine welding, fast speed, minimal heat-affected zones, high-quality welding, and material diversity. These attributes make it highly useful in applications requiring high-precision and micro-fine welding, such as in electronics manufacturing, medical device production, optical components, and other diverse fields.
Cost Influencing Factors for a Micro Plasma Welding Machine:
The cost or price of a micro plasma welding machine varies depending on the machine’s specifications and performance, the manufacturer and brand, and the market region. As a highly precise and specialized equipment, the price of a micro plasma welding machine can vary significantly based on accuracy and usage requirements. Specific price determinants include:
- Machine Specifications and Performance: The price will vary based on power, welding precision, speed, and automation level, with higher power, performance, precision, and automation typically costing more.
- Quality of Materials and Components: Machines made with high-quality materials and components are more durable and precise, but also more expensive.
- Manufacturer and Brand: Different manufacturers offer varied price ranges based on their market positioning. Renowned manufacturers usually command higher prices. Additionally, manufacturers providing excellent customer service and support might incur additional costs.
- Technology and Innovation: Costs for new technology development are reflected in the final price of machines that incorporate new technologies.
- Customization Requirements: Customization, especially complex designs, or additional fixtures, control systems, and automation equipment, can significantly increase manufacturing costs and the final price.
- Geographical Location: Prices may vary in different regions or countries due to taxes, tariffs, shipping costs, installation and maintenance fees, and varying standards for equipment safety and certification.
- Operating and Maintenance Costs: Machines with higher energy efficiency might have higher initial costs but lower long-term operational costs, particularly in regions with high energy prices. Similarly, machines that are easier to maintain and repair have lower long-term operational costs.
Overall, the cost of a micro plasma welding machine is influenced by a variety of factors, which can affect the price differently in various scenarios. For accurate pricing information, it’s recommended to contact welding equipment manufacturers or suppliers directly. They can recommend the most suitable equipment solutions based on your specific needs and budget constraints.
How to Choose a Micro Plasma Welding Machine Manufacturer and Supplier:
Selecting the right manufacturer and supplier for a Micro Plasma Welding Machine is a complex process that requires thorough communication and evaluation. Here are some tips and methods to consider when choosing a manufacturer and supplier for a micro plasma welding machine:
- Clarify Your Needs: Firstly, it’s crucial to clearly define your welding requirements before purchasing equipment. Determine the type of welding machine needed, performance specifications, production capacity, precision requirements, and any other special welding-related needs. This will help match you more effectively with the right supplier and product.
- Market Research: Conduct market research to find potential micro plasma welding machine manufacturers and suppliers. Utilize internet searches, industry trade shows, or professional welding equipment websites to gather information.
- Filter Potential Suppliers: Screen potential suppliers from your list. Consider their experience, product quality, technical support, and level of service. Also, consider their geographic location, as some industry clusters can offer more specialized and cost-effective services.
- Contact Suppliers: Reach out to potential suppliers with your requirements and ask for customized solutions, detailed equipment information, specifications, and quotes. Request their experience on similar projects, which can provide valuable references and help assess their professionalism and reliability. Efficient communication can be conducted via email, conference calls, or instant online chat tools.
- Compare Proposals and Quotes: Evaluate the equipment proposals and quotes provided by different suppliers. Consider equipment configuration, performance parameters, delivery time, technical support, warranty, and other comprehensive factors beyond price.
- Consider After-Sales Service: Ensure that the supplier offers good after-sales service, including training, maintenance, and repair support. Technical support is particularly important for welding equipment, which often requires on-site assembly and regular maintenance.
- Factory Visits: If possible, visit the supplier’s manufacturing facility to see their production process, quality control, and actual equipment manufacturing. This is particularly important when purchasing large equipment.
- Local Regulations and Standards: Before making a final decision, understand the local regulatory requirements and standards to ensure the chosen equipment complies with local laws and standards.
- Make a Decision: Based on your research, select the most suitable micro plasma welding machine manufacturer and supplier. Carefully review the contract terms and conditions before signing.
- Market Research and Communication: Detailed market research is advisable. If unsure about specific requirements or questions, contact potential suppliers for clarity. This not only helps define your needs but also gives an insight into the supplier’s expertise and service quality. Establish good communication with the supplier to ensure both parties’ needs and expectations are met.
In summary, a micro plasma welding machine is a specialized piece of equipment for micro-fine welding and high-precision applications, playing a significant role in key industry applications. The technology’s precision and controllability make it valuable for applications requiring precise welding. If you’re seeking information or looking to purchase a micro plasma welding machine, consider contacting Deewi Automation, which has extensive experience and proven solutions in this field. Want to know more.
Micro plasma welding video:
Common Questions and Answers about Micro Plasma Welding Machines:
Question 1: How does micro plasma welding differ from traditional welding methods, including TIG welding?
Answer 1: Micro plasma welding offers higher precision and control compared to traditional welding methods, making it ideal for manufacturing tiny components and precision assemblies. Compared to TIG welding (Tungsten Inert Gas welding), micro plasma welding has a higher energy density in the plasma arc, making it more suitable for welding small parts with high precision.
Question 2: How do I choose a micro plasma welding machine that suits my needs?
Answer 2: When selecting a micro plasma welding machine, first consider your welding needs, performance requirements, and budget. Then, consult with suppliers to get proposals, quotes, and recommendations to evaluate and determine the most suitable micro plasma welding machine for your specific requirements.
Question 3: Is training required to operate a micro plasma welding machine?
Answer 3: Yes, training is necessary for operating a micro plasma welding machine. It ensures that operators are familiar with the machine’s procedures and can safely and efficiently complete welding tasks.
Question 4: How are parameters set and controlled on a micro plasma welding machine?
Answer 4: Setting and controlling parameters on a micro plasma welding machine typically involve adjusting the arc current, voltage, wire feed speed, and welding speed, among others, to accommodate different welding tasks based on specific requirements.
Question 5: What should be noted for the maintenance of a micro plasma welding machine?
Answer 5: Maintenance of a micro plasma welding machine generally includes regular cleaning, calibration, and servicing of the machine. This involves cleaning nozzles and other areas prone to clogging, replacing the plasma gas and electrodes, and checking the cooling system, electrical circuits, and gas lines for any issues.
Question 6: What are the safety concerns when using a micro plasma welding machine?
Answer 6: Safety is paramount when using a micro plasma welding machine. It’s important to wear appropriate protective gear, ensure proper ventilation in the workspace, prevent gas leaks, and routinely check the electrical circuits for any damage or risk of electric shock to mitigate potential hazards.