Valve Cladding
Deewi Automation: Your Premier Manufacturer, Supplier, and Exporter of High-Quality Valve Cladding Machines.
What is valve cladding?
Valve cladding is a surface hardening technique that involves the fusion of wear-resistant or corrosion-resistant materials onto the surface of valve components to enhance their wear and corrosion resistance, among other properties. This technique can be used in the manufacturing or maintenance of valves. In industries with rigorous demands such as petrochemical, nuclear energy, and marine engineering, the valves are subjected to harsh operating conditions, such as high temperatures, high pressures, erosion, corrosion, and wear. These conditions necessitate higher performance from the valves. Through cladding technology, the performance of valves can be significantly improved, extending their service life, reducing equipment downtime, and ensuring long-term, stable operation of the equipment. Cladding technology can also be applied to the repair of severely worn or damaged valves, restoring their dimensions and shape. Moreover, the performance of the repaired valves can even surpass that of newly manufactured ones.
Where can valve cladding be performed?
Valve cladding processes such as laser cladding and plasma cladding are commonly employed, each with its unique characteristics and applications. Given the extensive use of valves in our daily industrial operations and production, the cladding process is incredibly widespread in the application of valves and their components. Specifically, this includes ball valves, custom-shaped ball valves, eccentric valves, safety valves, globe valves, bronze valves, power station valves, control valves, control valve bodies, control valve plugs, forged steel valves, forged steel valve rings, valve discs, valve bodies, valve stems, valve rings, valve cores, valve seats, valve inner holes, valve parts, valve cages, valve plugs, sealing surfaces, flat gate valves, flat gate valve seats, ball valve seats, ball valve bodies, triple-offset valve rings, sleeve control valves, wedge gate valves, wedge discs, instrument valves, gate valve bodies, gate valve discs, gate valve rings, gate valve seats, arched valve discs, grinding disc rings, wear rings, eccentric valve discs, and more. We have listed only the common valves and components that utilize cladding technology. If you have other needs, you are welcome to contact Deewi Automation.
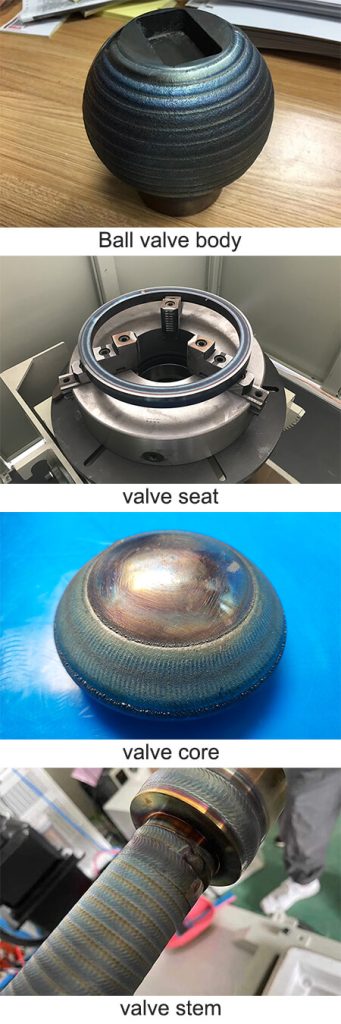
Quick Q&A – About Valve Cladding.
Regarding ‘Valve Cladding’, here are some common questions and their answers:
Valve Cladding Technology & Applications
Here, we’ll share insights onValve Cladding technology and its various applications. If you’re interested in these topics, we welcome you to join the discussion.
Deewi Automation Technology Co.,Ltd.
We are glad to offer technical solutions to people who are interested in our products. You just need to fill a form.
Get in touch with us today!