Applications of Laser Cladding Machines in Repairing Power Generation Equipment in the Electric Power Industry
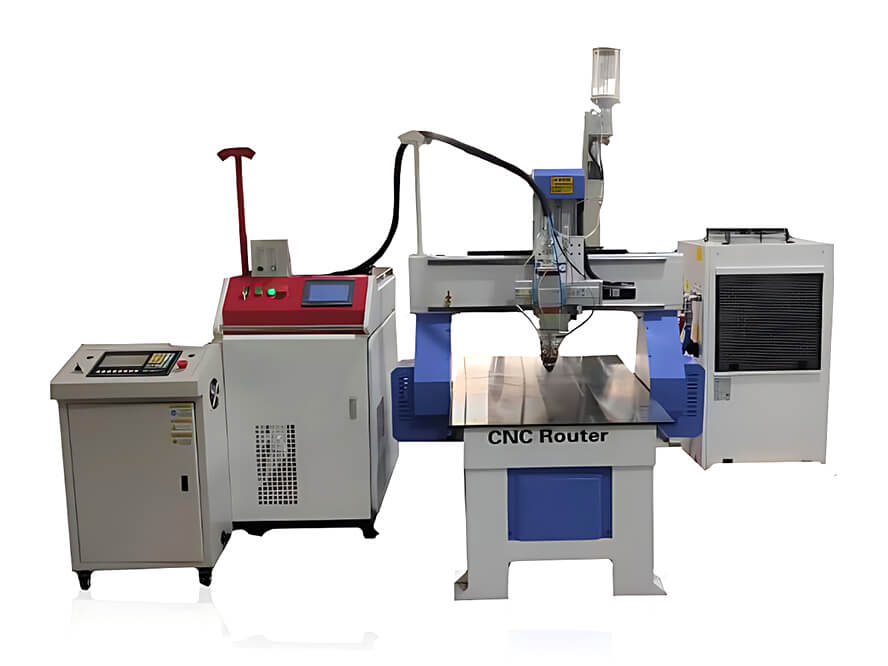
In the power industry, since power equipment is widely distributed and needs to operate continuously, the probability of damage to its parts is quite high. In harsh operating environments, components of power generation equipment inevitably face the test of gas, high temperature, high pressure, and corrosive media. Equipment that has been used for a long time, such as impellers, turbines, axles, etc. in wind/hydro power generation equipment, may be partially damaged due to aging. In order to extend the service life of these expensive production equipment, laser cladding machines provide an effective surface remanufacturing technology for repair. Especially for the blades of the generator set, the cost is extremely high. By reinstalling and reusing the blades repaired by thelaser cladding machine, the power generation cost of the power plant can be greatly reduced.
Laser cladding technology is an important method of material surface modification technology. It uses high-energy-density laser beams to quickly melt alloys with different compositions and properties on the surface of the base material, forming a completely different composition and properties on the surface of the base material. The rapid solidification process of the alloy layer. Under the action of rapid heat, the base body is minimally affected by heat and has no deformation. The molten layer alloy forms its own system, with dense structure, refined grains, increased hardness and toughness, and greatly improved surface properties. Laser cladding technology solves a series of technical problems such as thermal deformation and thermal fatigue damage that are inevitable during thermal processing such as traditional electric welding and argon arc welding.
Applications such as laser repair/laser remanufacturing of steam turbine rotors, laser repair of gear shafts, laser repair/laser remanufacturing of steam turbine blades demonstrate the wide application and effect of laser cladding machines in practice. Laser cladding has low dilution rate, dense structure, good combination of coating and substrate, and is reliable in use.
Judging from the current application of laser cladding machines, it is mainly used in three aspects:
- first, surface modification of materials, such as turbine blades, rollers, etc.;
- second, repair of parts, such as wind power spindles, planet carriers, planet wheels, etc.;
- third, It is rapid prototyping, which uses metal powder to be sintered and superimposed layer by layer to quickly create a model.
Laser cladding machines can also be used to repair damaged three-dimensional complex parts, which fully reflects the flexibility and advancement of laser remanufacturing technology.
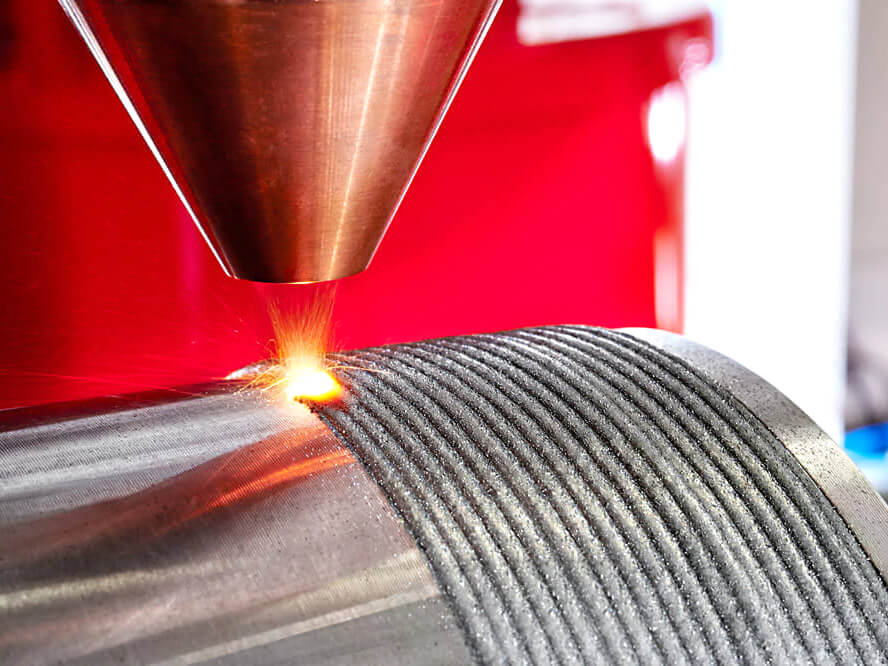
There are two types of laser cladding process methods –
01. Two-step method (preset method)
In this method, before the laser cladding process, the cladding material is first placed on the working surface, and then the laser is used to melt it and condense it to form a cladding layer. Methods of presetting cladding materials include:
- Preset coating layer: It is usually applied manually, which is the most economical and convenient. It uses a binder to mix the cladding powder into a paste and places it on the surface of the workpiece. After drying, laser cladding is performed. However, this method has low production efficiency and inconsistent cladding thickness, so it is not suitable for mass production.
- Preset sheet: Add a small amount of adhesive to the powder of the cladding material and mold it into a sheet, place it on the part of the workpiece that needs to be cladded, and then perform laser processing. This method has high powder utilization rate and stable quality, and is suitable for some deep-hole parts, such as small-diameter valve bodies. This method can obtain high-quality coatings.
02. One-step method (synchronous method).
This is a process in which the laser beam irradiates the workpiece while simultaneously delivering cladding material to the laser action area. There are two methods:
- Synchronous powder feeding method: Use a special jet powder feeding device to feed single or mixed powder into the molten pool, and control the amount of powder feeding and laser scanning speed to adjust the thickness of the cladding layer. Because the loose powder has a large absorption rate of laser and high thermal efficiency, a thicker cladding layer can be obtained than other methods, and it is easy to realize automation.
- Synchronous wire feeding method: The process principle of this method is the same as that of the synchronous powder feeding method, but the cladding material is pre-processed into wire material or filled wire material is used. This method is convenient and does not waste material, and it is easier to ensure the uniformity of the composition of the cladding layer. Especially when the cladding layer is a composite material, the quality of the cladding layer will not be affected by differences in powder specific gravity or particle size, and the wire Detailed preheating of the material can increase the cladding rate. However, the surface of the wire is smooth, the reflection of laser is strong, and the laser utilization rate is relatively low; in addition, the wire manufacturing process is complicated and there are few varieties and specifications.
As an important supporting technology representative product of green remanufacturing technology, laser cladding machine is very in line with the current sustainable development trend. Deewi has achieved international advanced levels in basic theoretical research on technical engineering and has made great contributions to the development of laser cladding technology.